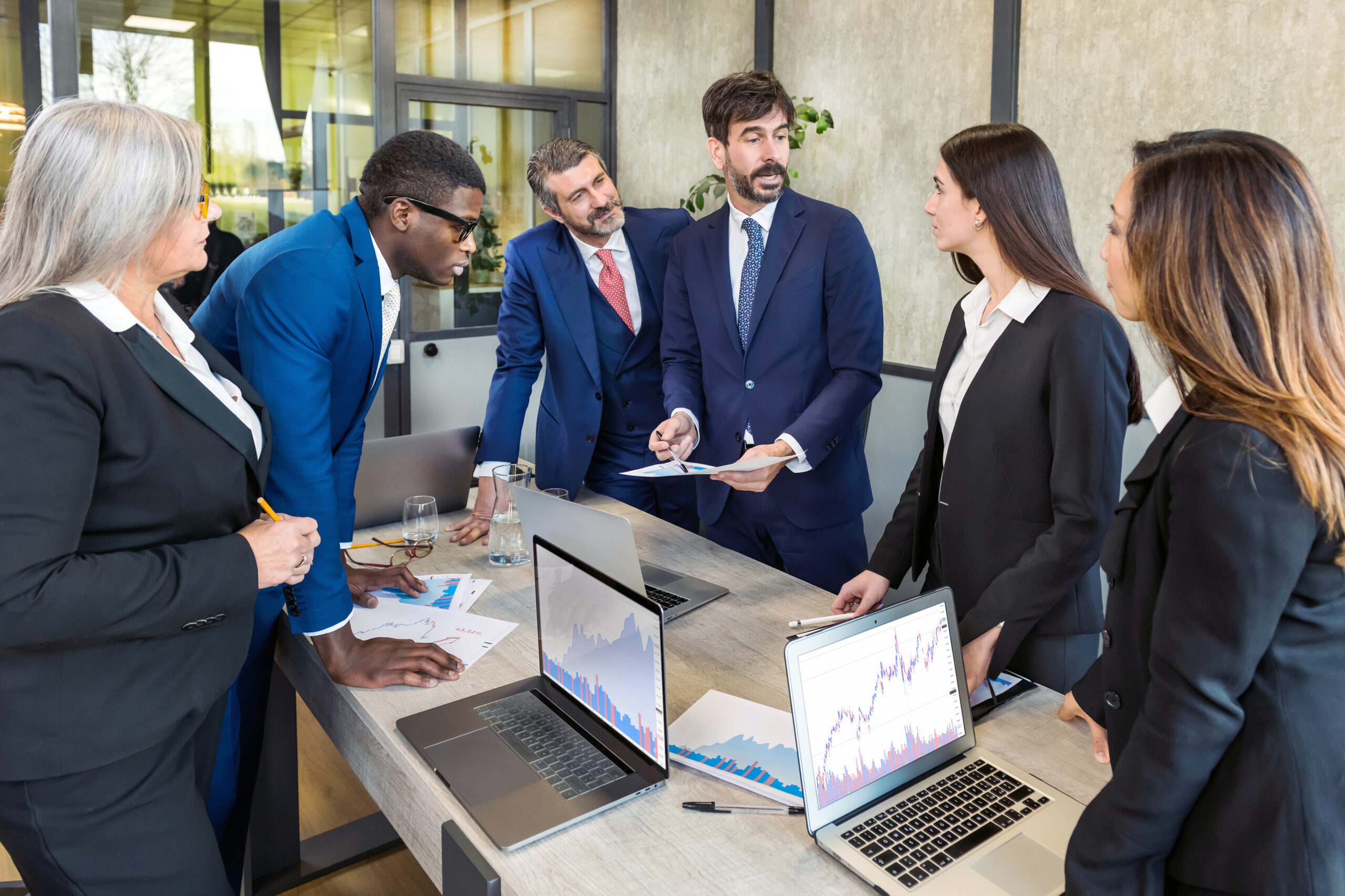
Equipment assessment plays a crucial role in maintaining operational efficiency and preventing costly breakdowns. At End2EndLogix, we offer comprehensive products and services to help businesses optimize their maintenance strategies. Our expert team conducts thorough equipment evaluations, providing valuable insights to extend the lifespan of your assets and reduce downtime. For more information about our services, contact us today. In this article, we’ll explore the various aspects of equipment assessment and its impact on maintenance programs.
Understanding the Impact of Regular Equipment Assessment
Regular equipment assessment forms the cornerstone of effective maintenance strategies. By systematically evaluating your end2endlogix commercial display units, you gain valuable insights into their performance and condition. This proactive approach allows you to address potential issues before they escalate, ensuring optimal functionality and longevity. Through routine assessments, you not only safeguard against unexpected breakdowns but also implement targeted preventive measures that significantly extend the lifespan of your products and services equipment.
Identifying Potential Failures Before They Occur
Regular equipment assessments enable you to spot early warning signs of potential failures in your commercial display units. By conducting thorough inspections and analyzing performance data, you can identify subtle changes or degradation that might lead to future breakdowns. This foresight allows you to schedule timely repairs or replacements, minimizing costly downtime and ensuring your displays consistently meet performance standards. contact us to learn more about our end2endlogix products and services.
Extending the Lifespan of Your Equipment With Preventive Care
Preventive care significantly extends the lifespan of your commercial display units. By implementing a regular maintenance schedule, you address minor issues before they become major problems. This proactive approach includes cleaning, lubricating, and adjusting components as needed. You also replace worn parts before they fail, ensuring optimal performance and reliability.
- Conduct regular inspections
- Clean and lubricate components
- Replace worn parts proactively
- Adjust settings for optimal performance
- Document maintenance activities
Strategies for Conducting Effective Equipment Assessments
Effective equipment assessments require a systematic approach and skilled personnel. To maximize the benefits of your assessment program, you need to establish clear procedures and equip your team with the necessary knowledge. By implementing standardized assessment protocols and providing comprehensive training, you ensure consistency, accuracy, and efficiency in evaluating your commercial display units. These strategies not only streamline the assessment process but also enhance the overall effectiveness of your maintenance efforts.
Implementing a Standardized Assessment Procedure
Implement a standardized assessment procedure to ensure consistent evaluations of your commercial display units. Develop a detailed checklist that covers all critical components and performance metrics. Train your team to follow this procedure meticulously, documenting their findings in a uniform format for easy comparison and trend analysis.
Training Your Team on the Latest Assessment Techniques
Train your team on the latest assessment techniques to enhance the accuracy and efficiency of equipment evaluations. Provide comprehensive training programs that cover both theoretical knowledge and hands-on practice with your specific commercial display units. Keep your team updated on emerging technologies and methodologies in equipment assessment to ensure they remain at the forefront of maintenance practices.
- Develop comprehensive training programs
- Combine theoretical knowledge with hands-on practice
- Stay updated on emerging assessment technologies
- Conduct regular refresher courses
- Encourage continuous learning and skill development
How Technology Is Changing Equipment Maintenance
Technology revolutionizes equipment maintenance for commercial display units. Advanced tools and systems transform how you assess, monitor, and maintain your assets. Internet of Things (IoT) devices enable real-time data collection and analysis, facilitating predictive maintenance strategies. Artificial Intelligence (AI) algorithms process vast amounts of information, enhancing the accuracy and efficiency of equipment assessments. These technological advancements empower you to make data-driven decisions, optimize maintenance schedules, and minimize downtime.
The Rise of IoT in Predictive Maintenance Strategies
IoT devices transform predictive maintenance for your commercial display units. These smart sensors continuously monitor equipment performance, collecting real-time data on temperature, vibration, and other critical parameters. By analyzing this data, you can predict potential failures and schedule maintenance precisely when needed, reducing unnecessary downtime and extending equipment life.
Leveraging AI for Enhanced Accuracy in Assessments
AI enhances the accuracy of your commercial display unit assessments. By processing vast amounts of historical and real-time data, AI algorithms identify subtle patterns and anomalies that human operators might miss. You can use these insights to make more precise predictions about equipment performance and potential failures, leading to more effective maintenance strategies and reduced downtime.
Cost-Benefit Analysis of Routine Equipment Checks
Routine equipment checks for your commercial display units offer substantial financial benefits. By systematically evaluating the condition and performance of your assets, you gain valuable insights that translate into tangible cost savings. These regular assessments help you quantify the financial impact of avoiding unexpected downtime and compare the long-term benefits of investing in maintenance versus the expenses associated with equipment replacement. Understanding these economic implications empowers you to make informed decisions about your maintenance strategies, ultimately optimizing your operational efficiency and budget allocation.
Calculating Savings From Avoided Downtime
Calculate the savings from avoided downtime by analyzing the potential costs of equipment failure. Estimate the revenue loss per hour of downtime, including lost production, labor costs, and potential damage to customer relationships. Factor in the expenses of emergency repairs or replacements. Compare these costs to the investment in routine assessments and preventive maintenance to quantify your savings.
Investing in Maintenance vs. The Cost of Replacement
Conduct a thorough cost analysis to compare the investment in maintenance against the expense of replacing your commercial display units. Calculate the total cost of ownership for each approach, including initial purchase price, maintenance expenses, operational costs, and projected lifespan. This analysis helps you determine the most cost-effective strategy for managing your equipment, allowing you to make informed decisions about whether to continue maintaining existing units or invest in new ones.
Case Studies on Successful Maintenance Programs
You’ll find valuable insights from a major retail chain that implemented a comprehensive equipment assessment program for their commercial display units. By conducting regular evaluations and preventive maintenance, they reduced unexpected breakdowns by 75% and extended the average lifespan of their displays by three years. This proactive approach resulted in significant cost savings and improved customer experience.
A leading electronics manufacturer’s case study demonstrates the power of data-driven assessments. They integrated IoT sensors into their display units, enabling real-time monitoring and predictive maintenance. This strategy allowed them to identify potential issues before they escalated, reducing repair costs by 40% and minimizing downtime across their network of retail partners.
An airport’s success story highlights the importance of staff training in equipment assessment. By investing in comprehensive training programs for their maintenance team, they improved the accuracy of their display unit evaluations by 60%. This enhanced capability led to more targeted maintenance interventions, resulting in a 30% reduction in overall maintenance costs and a significant improvement in traveler satisfaction scores.
Conclusion
Regular equipment assessment plays a crucial role in maintaining commercial display units effectively. By conducting systematic evaluations, businesses can identify potential issues early, implement preventive measures, and extend the lifespan of their equipment. Advanced technologies like IoT and AI enhance the accuracy and efficiency of these assessments, enabling data-driven maintenance strategies. Ultimately, a well-executed equipment assessment program leads to significant cost savings, reduced downtime, and improved operational efficiency for businesses across various industries.
Share This Story, Choose Your Platform!
Get In Touch
Phone: (847) 722-6942
Email: sales@end2endlogix.com
Web: end2endlogix.com