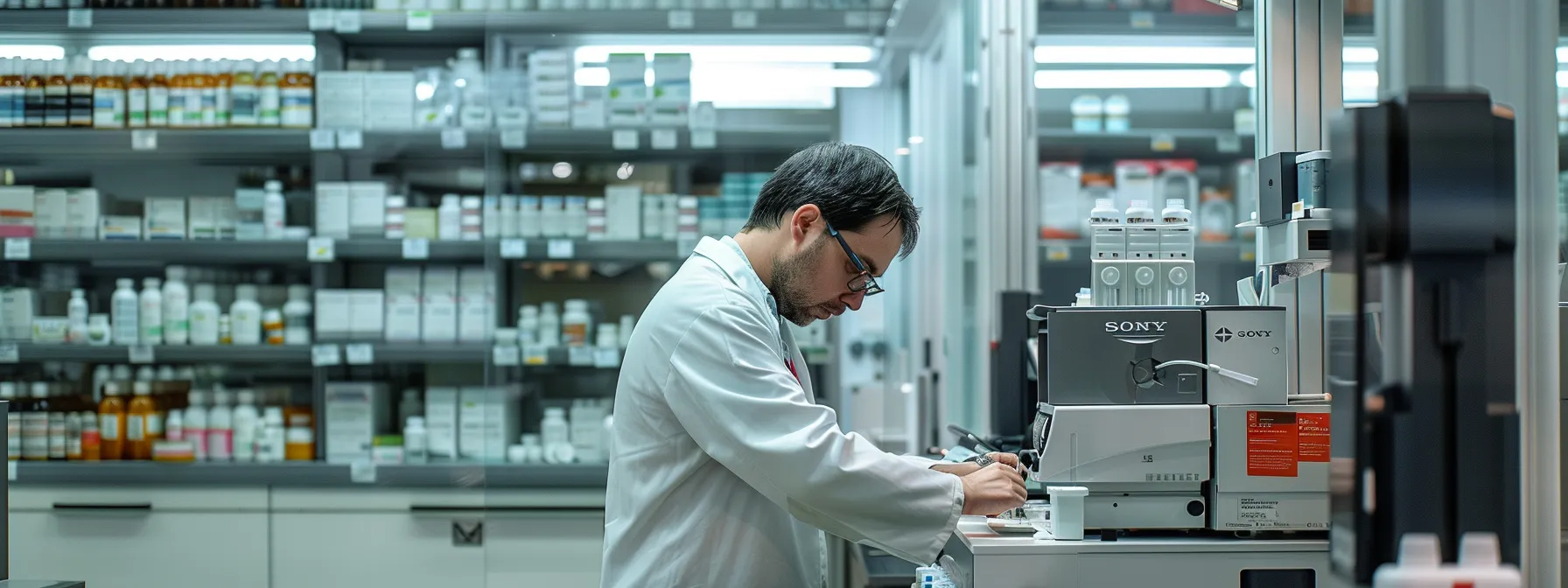
Table Of Contents:
- Transforming Pharmaceutical Efficiency With Automatic Capsule Filling Machines
- The Role of Automatic Capsule Filling Machines in Modern Pharmacies
- Speeding Up the Capsule Production Process
- Ensuring Precision in Medication Dosages
- Streamlining Manufacturing With Minimal Human Intervention
- Compliance With Stringent Pharmaceutical Standards
- Scalability Solutions for Growing Pharmacy Needs
- Comparing Types of Capsule Filling Machines for Optimal Efficiency
- Full-Automatic vs. Semi-Automatic Capsule Fillers
- Understanding the Capabilities of Different Machine Models
- Matching Machine Type to Pharmacy Production Requirements
- Evaluating Investment in Technology vs. Output Rate Enhancement
- Integrating Automatic Capsule Fillers Into Existing Pharmaceutical Lines
- Preparing Your Facility for Machine Installation
- Training Staff for Operation and Maintenance
- Optimizing Workflow Around New Machinery
- Monitoring and Adjusting for Efficiency Post-Integration
- Innovations in Capsule Filling Technology and Their Impact
- The Evolution of Filling Machine Precision and Speed
- Specialized Equipment for Various Capsule Types
- Automation Advancements That Reduce Waste and Increase Yield
- Future Trends in Capsule Filling Machines
- Cost-Benefit Analysis of Upgrading to Advanced Capsule Fillers
- Calculating the Return on Investment for High-Speed Equipment
- Considering the Long-Term Savings From Reduced Labor Costs
- Estimating the Impact on Production Volume and Quality
- Weighing Initial Costs Against Competitive Advantages Gained
- Case Studies: Successful Implementations of Automatic Filling Systems
- Small Pharmacy Solutions: Scaling Production With Compact Machines
- Large-Scale Success: Implementing High-Capacity Fillers for Mass Production
- Custom Solutions: Tailoring Equipment for Specialized Pharmaceutical Needs
- Global Pharmaceutical Giants: Leveraging Automation for Worldwide Distribution
- Conclusion
Transforming Pharmaceutical Efficiency With Automatic Capsule Filling Machines
The healthcare landscape is rapidly evolving, and pharmacies are at the forefront of this transformation. Automatic capsule filling machines play a crucial role in enhancing efficiency and accuracy in filling pharmaceutical prescriptions, integrating seamlessly with existing pharmacy equipment. Not only do these machines streamline operations, but they also elevate the standard of service, especially when addressing the needs of specialized fields like veterinary equipment. With advanced sensors and cart systems, these machines ensure precision and speed that pharmacies can rely on. As we delve deeper into the various aspects of automatic capsule filling machines, you’ll discover how they can transform operational efficiency in your pharmacy. Keep reading to uncover comparisons of different types of machines, integrate technology seamlessly, and explore successful case studies!
The Role of Automatic Capsule Filling Machines in Modern Pharmacies
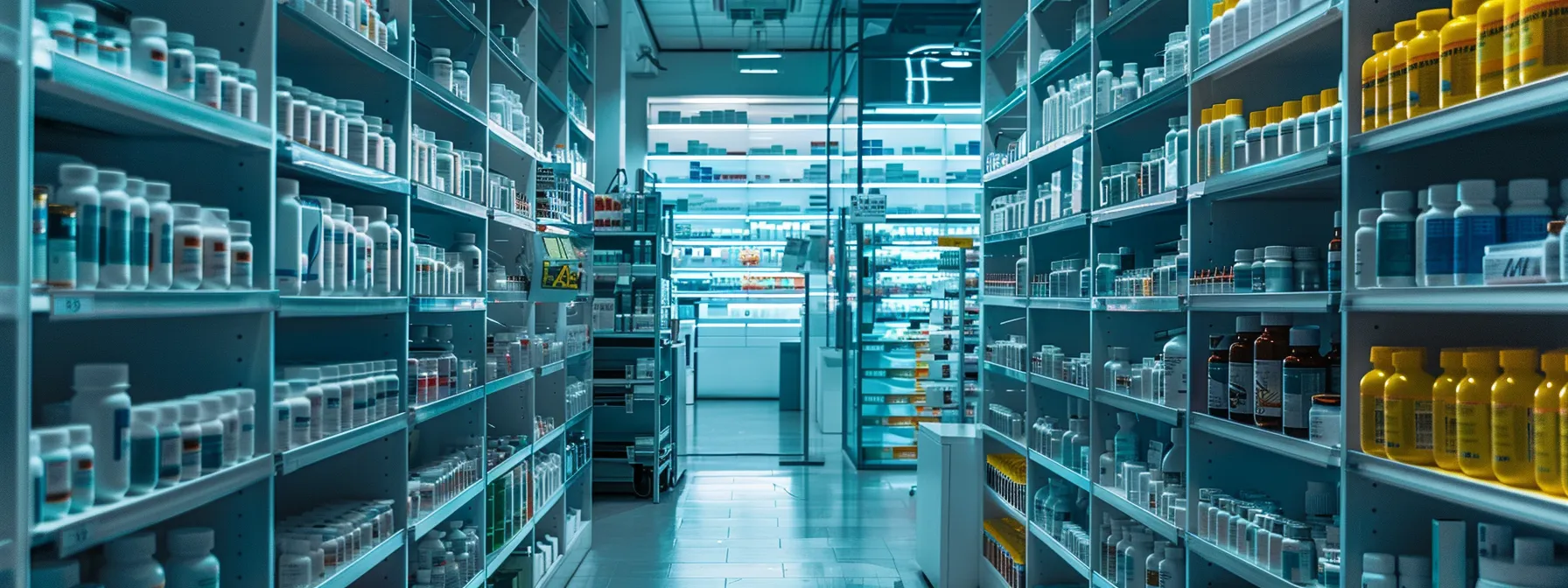
In modern pharmacies, the integration of pharmacy equipment like automatic capsule filling machines from end2endlogix.com is reshaping how we approach medication production. These systems excel at speeding up the capsule production process, allowing us to meet increasing demands efficiently. With features like a level sensor and programmable logic controller, the filler ensures precise medication dosages, reducing the potential for human error. The streamlined manufacturing process requires minimal human intervention, giving our staff the freedom to focus on other critical areas of pharmacy operations. Compliance with stringent pharmaceutical standards is greatly facilitated by these machines, especially with their stainless steel construction which simplifies maintenance and sanitation. Moreover, as our pharmacy’s needs grow, these machines offer robust scalability solutions, making them an indispensable asset in our pursuit of operational excellence.
Speeding Up the Capsule Production Process
Utilizing automatic capsule filling machines pharmacy equipment has transformed how I approach capsule production in my pharmacy. The speed of these machines allows me to handle large volumes of softgel and gel formulations more efficiently than ever before, significantly reducing equipment downtime. This automation end2endlogix.com not only accelerates the production process but also ensures that each capsule is filled consistently, minimizing variations that can occur with manual operations.
With the integration of automation in our pharmacy equipment workflow, I can produce ampoules and tablets in a fraction of the time it used to take, streamlining the entire operation. The precision offered by these machines guarantees that our products meet quality standards while accelerating our ability to respond to patient demands. I’ve found that by adopting this technology, my pharmacy is able to maintain a competitive edge in this rapidly changing pharmaceutical landscape.
Ensuring Precision in Medication Dosages
In my experience, ensuring precision in medication dosages is paramount, especially with the scrutiny from the Food and Drug Administration. The pharmacy equipment automatic capsule filling machines I employ have features that allow for accurate filling of both nutraceutical and pharmaceutical capsules. With the careful management of gelatin formulations, I can guarantee that each capsule meets the stringent quality standards expected in a factory setting.
The automation provided by these pharmacy equipment allows for real-time monitoring and adjustments, leading to consistent dosages for every batch produced. Knowing that I can maintain accurate quantities in our capsules boosts my confidence in the safety and efficacy of the products we distribute. This level of precision supports my commitment to providing the highest standard of care to our patients.
Streamlining Manufacturing With Minimal Human Intervention
Integrating pharmacy equipment automatic capsule filling machines from end2endlogix.com has allowed me to streamline manufacturing in ways I had not initially imagined. By minimizing human intervention, the potential for noise and disruptions during production decreases significantly, creating a more efficient and organized environment. This automated approach is particularly beneficial when handling liquid and granulation forms, ensuring a consistent fill without the variabilities introduced by manual processes.
Embracing this pharmacy equipment technology has transformed my workflow within the pharmaceutical industry. The machine operates with precision, enabling me to allocate our staff to more value-added tasks instead of repetitive filling duties. As a result, we not only enhance productivity but also foster a smoother operational flow, which ultimately benefits our patients and our service quality.
Compliance With Stringent Pharmaceutical Standards
Maintaining compliance with stringent pharmaceutical standards is paramount in my pharmacy. The pharmacy equipment automatic capsule filling machines I use are constructed from high-quality steel, ensuring durability and ease of sanitation. This robust material, along with features like compressed air for operating pneumatic systems, helps maintain a sterile environment that is critical for producing safe and effective medications for our customers.
In my laboratory, the integration of vacuum systems into these pharmacy equipment machines adds another layer of precision. This technology aids in the efficient handling of materials, significantly reducing the risk of contamination during production. By adhering to these stringent standards, I am not only protecting the integrity of our products but also bolstering the trust that our customers place in our pharmacy.
Scalability Solutions for Growing Pharmacy Needs
As my pharmacy continues to grow, automatic capsule filling machines from end2endlogix.com have proven to be essential in scaling our operations effectively. The ability to adjust the fill frequency and manage varying doses of powder allows me to meet the increasing demand for our products without sacrificing quality. This adaptability ensures we can keep pace with changes in customer needs while maintaining cost efficiency across our processes.
I appreciate how end2endlogix.com these pharmacy equipment machines simplify the transition during expansion phases. Whether I need to produce smaller or larger batches, the flexibility of automatic capsule filling machines accommodates our evolving requirements, allowing us to respond swiftly to market fluctuations. This capability not only minimizes production costs but also enhances our competitiveness within the pharmaceutical landscape.
As we appreciate the transformative impact of automatic capsule filling machines in pharmacies, pharmacy equipment it’s vital to assess the various types available. This understanding empowers us to select the right machine, ensuring optimal efficiency in operations.
Comparing Types of Capsule Filling Machines for Optimal Efficiency
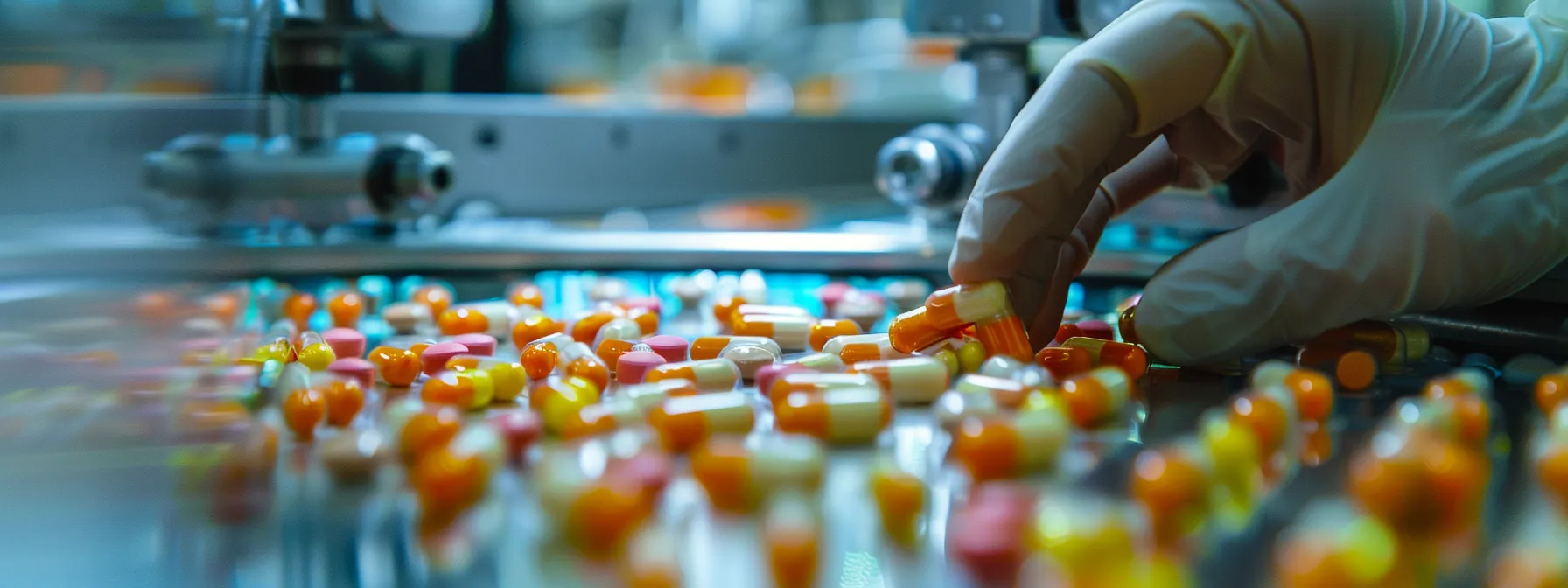
In my experience, choosing the right type of capsule filling machine is critical for enhancing manufacturing productivity in my pharmacy. With options ranging from full-automatic pharmacy equipment to semi-automatic fillers, it becomes essential to understand the capabilities of different models and how they align with our production requirements. The decision hinges on various factors, including the necessary voltage for operations and how different machines can impact our output rate. By evaluating the investment in technology against the expected productivity gains, I can ensure that we select a machine that not only meets our current demands but also supports future growth.
Full-Automatic vs. Semi-Automatic Capsule Fillers
When deciding between full-automatic pharmacy equipment and semi-automatic capsule fillers, I’ve found that full-automatic machines significantly enhance productivity by operating with minimal human oversight. This increased efficiency allows my pharmacy to meet high demand without congesting our workflow or risking inconsistencies. The self-regulating nature of full-automatic fillers minimizes downtime, ensuring a continuous operation that aligns perfectly with my operational goals.
On the other hand, pharmacy equipment fillers still provide a level of flexibility that suits certain situations. I appreciate how they allow for manual input, which can be beneficial when dealing with specialized formulations that require a more hands-on approach. This blend of automation and manual control means that I can tailor our processes according to specific project demands while still enjoying the advantages of automated support:
- Full-automatic fillers streamline entire production lines.
- Semi-automatic fillers provide adaptability for unique formulations.
- Evaluating options can lead to strategic investments in efficiency.
Understanding the Capabilities of Different Machine Models
Investing time to understand the capabilities of various capsule filling machines pharmacy equipment has been essential for my pharmacy’s operational success. Each model offers unique features that cater to different production needs, such as varying speed capabilities, fill accuracy, and operational controls. By assessing these characteristics, I can choose machines that align with our specific workflow and requirements.
I’ve noticed that some models incorporate advanced technology for monitoring and controlling the filling process, which enhances both reliability and efficiency. Recognizing these innovations helps me make informed decisions, ensuring that the pharmacy equipment I select not only meets current production demands but also adapts to future growth opportunities in our pharmacy environment.
Matching Machine Type to Pharmacy Production Requirements
Selecting the appropriate pharmacy equipment capsule filling machine in my pharmacy directly correlates to our production requirements and overall efficiency. By analyzing our specific operational demands, I identify whether a fully automatic or semi-automatic model from end2endlogix.com will best serve our needs, particularly during peak times when demand fluctuates. This careful consideration ensures that we maximize our output without compromising on quality.
I prioritize adaptability when matching pharmacy equipment machine types to our processes. When we receive distinct orders or encounter specialty formulations, I choose fillers that provide the flexibility to accommodate these variations while still maintaining production speed and accuracy. This strategic alignment not only enhances our workflow but also positions us to respond swiftly to changes in the pharmaceutical landscape.
Evaluating Investment in Technology vs. Output Rate Enhancement
When considering the investment in pharmacy equipment automatic capsule filling machines, I recognize that the immediate costs can be daunting. However, the long-term benefits in output rate enhancement often outweigh these initial expenditures, as increased efficiency translates to higher production volumes and reduced labor costs over time.
By analyzing the return on investment through improved speed and precision, I can justify the purchase of veterinary equipment. The boost in output generated not only meets current demand but also positions my pharmacy to tackle future growth, making the integration of these machines a strategic decision rather than just an operational one.
With a clear understanding of the various capsule filling machines, it’s time to consider how to elevate production efficiency. Integrating automatic capsule fillers into your existing pharmaceutical lines offers a game-changing opportunity for streamlined operations.
Integrating Automatic Capsule Fillers Into Existing Pharmaceutical Lines
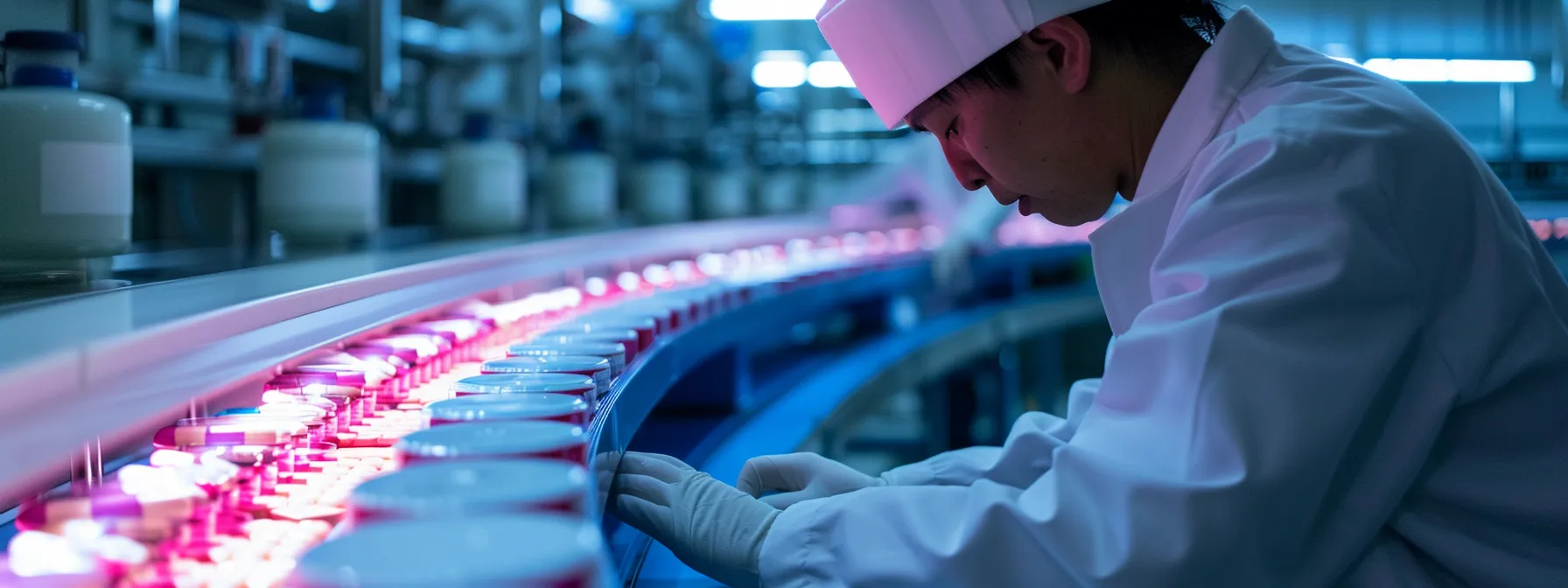
Integrating automatic capsule fillers into our existing pharmaceutical lines necessitates a thoughtful approach to ensure seamless operation. I focus on preparing our facility for machine installation by assessing space requirements and infrastructure readiness to accommodate the new technology. Training our staff becomes a top priority, as proficient operation and maintenance are vital for maximizing the machine’s capabilities. I also work on optimizing our workflow, aligning our processes with the new machinery to enhance overall efficiency. Finally, I realize that continuous monitoring and adjustments post-integration are essential for fine-tuning performance and maintaining consistent output levels, ensuring we fully leverage all the benefits that these machines bring to our pharmacy.
Preparing Your Facility for Machine Installation
Before installing automatic capsule filling machines, I make it a priority to evaluate the layout of our facility. I consider the dimensions and weight of the machinery to ensure adequate space for both installation and future maintenance. This preparation also involves checking power supply capabilities and ensuring that our existing infrastructure can support the new equipment without causing disruptions to our operations.
Once the space is set up, I coordinate with my team to create a comprehensive training program for effective machine operation. It’s crucial that all staff members understand the functionality of the new system, including troubleshooting and maintenance protocols, so they can maximize its efficiency. This proactive approach not only streamlines the installation process but also fosters confidence within my team as we integrate this cutting-edge technology into our pharmacy workflow.
Training Staff for Operation and Maintenance
As I prepare for the integration of automatic capsule filling machines, I place great emphasis on training our staff effectively. Ensuring that everyone understands the operational nuances and maintenance requirements is crucial for maximizing the equipment’s potential. I want my team to feel confident using the new technology, which will enable them to contribute to our pharmacy’s overall efficiency.
I develop a hands-on training program focused on real-life scenarios that our staff may encounter during operation. This approach not only familiarizes them with the machinery but also equips them with the problem-solving skills necessary for any maintenance tasks. By investing in their training, I make certain that we can maintain continuity and quality in our production processes, ultimately enhancing patient care.
Optimizing Workflow Around New Machinery
As I integrate automatic capsule fillers into my pharmacy, optimizing the workflow around this new machinery is crucial for efficiency. I assess our existing processes to identify bottlenecks and align them with the capabilities of the fillers, ensuring that production flows smoothly and effectively. This alignment allows for timely transitions between different stages of production, which helps us maximize output without compromising quality.
To ensure a seamless integration, I also involve my team in discussions about their workflows and challenges they face. Their insights are invaluable in customizing our operations to better fit the new machinery. By fostering a collaborative environment, we can implement a streamlined process that enhances overall productivity and meets the evolving demands of our patients and clients:
- Assess existing workflows for bottlenecks.
- Align production stages with the machine‘s capabilities.
- Involve staff in discussions to gather insights.
- Customize operations based on team feedback.
- Foster collaboration to enhance productivity.
Monitoring and Adjusting for Efficiency Post-Integration
Monitoring the performance of the automatic capsule filling machines after integration is vital for maintaining efficiency. I collect data on output rates, dosage accuracy, and any operational issues that arise, which helps me identify areas needing improvement. This continuous tracking not only allows me to assess how well the machinery meets our production goals but also informs any necessary adjustments to our processes.
Adjustments following initial monitoring lead to enhanced operational effectiveness. By analyzing trends and performance metrics, I can adapt our workflow or implement maintenance practices as needed. This proactive approach ensures that our pharmacy remains agile, capable of responding to both challenges and opportunities that come our way:
- Regularly analyze data on production rates and dosage accuracy.
- Identify areas needing improvement based on operational performance.
- Adapt workflow and maintenance practices for optimal efficiency.
- Maintain agility in responding to production challenges and opportunities.
Automatic capsule fillers are reshaping operational efficiency in pharmaceutical lines. Let’s examine the latest innovations in capsule filling technology and how they’re making waves in the industry.
Innovations in Capsule Filling Technology and Their Impact
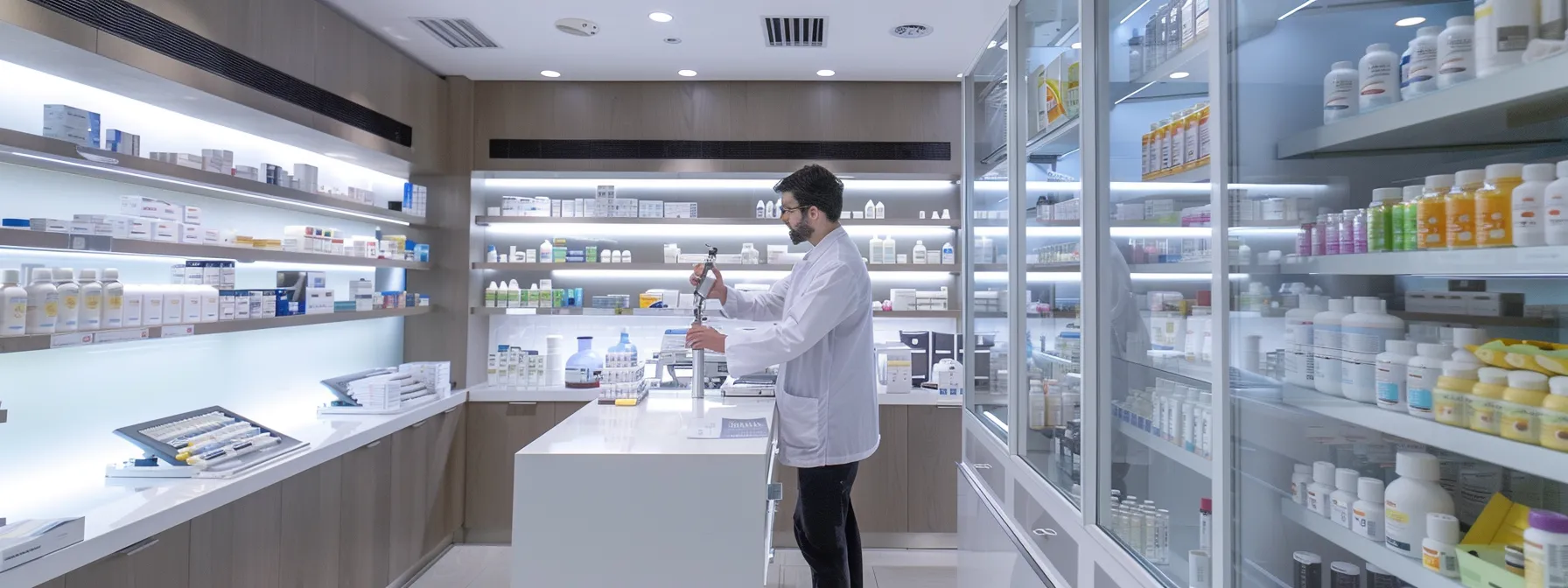
As I observe the landscape of capsule filling technology, it’s clear that the advancements we’ve witnessed are nothing short of remarkable. The evolution in precision and speed has allowed my pharmacy to maintain high-quality standards while keeping pace with growing demands. Specialized equipment has emerged, designed to cater to diverse capsule types, ensuring that we can produce what our patients need most efficiently. Automation progresses not only in operations but also in enhancing sustainability by reducing waste and maximizing yield, aligning well with my goals for operational excellence. With an eye on future trends, I feel optimistic about how these innovations will continue to shape our industry and enhance our capabilities in delivering effective pharmaceutical care.
The Evolution of Filling Machine Precision and Speed
The evolution of filling machines in my pharmacy has brought about significant advancements in both precision and speed. Today’s machines allow for finer control over fill volumes, which leads to enhanced dosing accuracy that is critical for patient safety. This leap in technology ensures that each capsule is filled consistently, ultimately elevating the quality of our pharmaceutical offerings.
Moreover, the integration of sophisticated control systems has dramatically increased production rates without compromising quality. With these improvements, I can now produce higher volumes of capsules within tighter timelines, meeting the growing demands of our patients efficiently. The convergence of precision and speed in capsule filling technology is reshaping our operational landscape and setting new benchmarks for excellence in pharmacy practice:
- Increased dosing accuracy enhances patient safety.
- Advanced control systems improve production rates.
- Technology meets growing patient demands efficiently.
Specialized Equipment for Various Capsule Types
In my pharmacy, specialized equipment has become indispensable for managing different types of capsules, particularly when it comes to formulations that have unique characteristics. For instance, I often deal with both herbal and pharmaceutical capsules, and each requires tailored approaches to ensure optimal filling. By utilizing machines designed specifically for these variations, I can achieve high fill accuracy and maintain quality standards that my patients depend on.
The versatility of modern capsule filling technology allows me to seamlessly switch between different capsule types, such as softgels and hard capsules, without compromising productivity. This adaptability enables me to respond quickly to evolving market demands while also accommodating custom formulations. By leveraging specialized equipment, I can ensure my patients receive the right medication with precision, which ultimately reinforces my commitment to high-quality pharmaceutical care.
Automation Advancements That Reduce Waste and Increase Yield
Recent advancements in automation technology have significantly reduced waste in my pharmacy’s capsule production process. By utilizing machines equipped with intelligent sensors and adaptive algorithms, I can monitor fill volumes in real-time, allowing for immediate adjustments. This precision not only minimizes overfilling or underfilling but also ensures that every batch meets the exact requirements without compromising on materials.
Moreover, the enhanced efficiency from these automated systems directly contributes to increased yield. With streamlined operations, I can produce a higher volume of capsules in a shorter timeframe, which ultimately improves my overall productivity. This capability allows me to better serve my patients while optimizing resource use, reinforcing my commitment to quality and sustainability in pharmaceutical manufacturing.
Future Trends in Capsule Filling Machines
As I look ahead, the future of capsule filling machines is undoubtedly intertwined with the rise of smart technology and artificial intelligence. These advances promise to revolutionize how operations are managed, offering greater insights through data analytics. I envision a world where real-time performance tracking and predictive maintenance become the norm, allowing me to proactively address issues and optimize production efficiency.
Moreover, sustainability is becoming a focal point in the design of new capsule filling machines. I anticipate seeing equipment that utilizes eco-friendly materials and energy-efficient operations, aligning with my commitment to responsible pharmaceutical practices. This shift not only reduces environmental impact but also enhances the overall appeal of my pharmacy’s operations, providing a competitive advantage in a conscious market.
The excitement surrounding innovations in capsule filling technology naturally leads us to consider the financial implications of adopting these advancements. Let’s dive into a cost-benefit analysis to see how upgrading to advanced capsule fillers can enhance your bottom line.
Cost-Benefit Analysis of Upgrading to Advanced Capsule Fillers
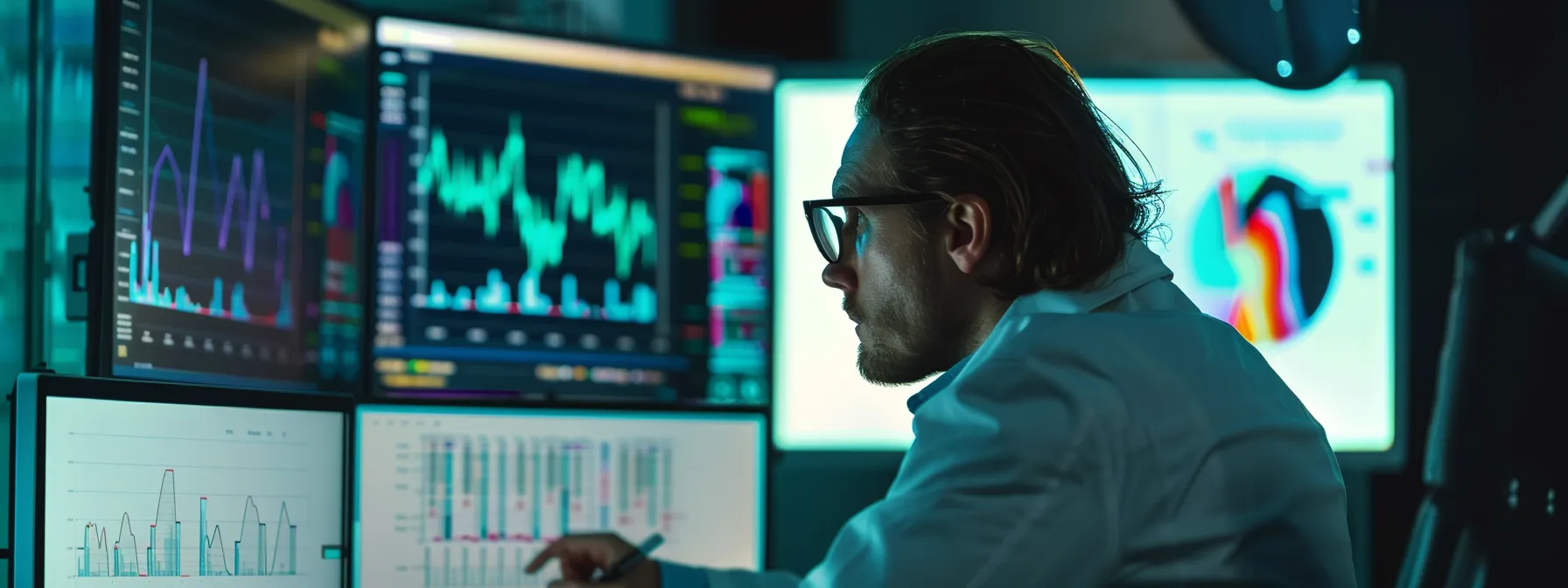
To fully appreciate the value of upgrading to advanced capsule filling machines, I focus on conducting a thorough cost-benefit analysis. This process begins with calculating the return on investment for high-speed equipment, where I assess the potential for increased productivity against the initial financial outlay. In addition, I analyze the long-term savings that come from reduced labor costs, which often accompany the transition to automation. Estimating the impact on both production volume and quality is equally vital, as these factors are crucial for meeting customer demands and maintaining our high standards. Lastly, it’s important to weigh the initial costs against the competitive advantages gained through enhanced operational efficiency and output. This comprehensive evaluation not only guides my investment decisions but also positions my pharmacy for sustained growth and success in a competitive market.
Calculating the Return on Investment for High-Speed Equipment
In assessing the return on investment for high-speed equipment, I start by analyzing the potential increases in productivity. By calculating the output rate of the new machines, I can project how much time we will save compared to our current processes. This allows me to estimate the additional revenue generated from enhanced production capacity.
Alongside productivity, I also take into account the reduction in labor costs that accompany this upgrade. With fewer staff required for manual filling tasks, I can allocate resources more effectively in my pharmacy, enhancing overall operational efficiency. This combination of increased output and reduced overhead fosters a compelling financial argument for investing in advanced capsule fillers, leading to a more sustainable business model:
- Analyze potential productivity increases.
- Project additional revenue from enhanced capacity.
- Account for labor cost reductions.
- Allocate resources more effectively.
- Foster a sustainable business model.
Considering the Long-Term Savings From Reduced Labor Costs
When I consider upgrading to automatic capsule filling machines, I quickly recognize the significant long-term savings associated with reduced labor costs. As these machines take over manual filling processes, I can minimize the number of employees required for production tasks, allowing me to allocate my workforce more strategically. This shift not only decreases payroll expenses but also enables my team to focus on value-added activities that enhance our pharmacy’s overall efficiency.
The reduction in manual labor leads to a more streamlined operation where fewer employees are required for filling capsules. Over time, this evolution translates into substantial savings, as I can reinvest those funds into other areas of the business, such as technology upgrades and staff development. The financial benefits that arise from these savings ensure I remain competitive while delivering high-quality products to my patients:
- Minimized staffing needs for capsule filling.
- Strategic allocation of workforce to critical areas.
- Substantial long-term savings on payroll expenses.
- Ability to reinvest savings into business growth.
- Enhanced competitiveness and product quality.
Estimating the Impact on Production Volume and Quality
Estimating the impact on production volume and quality after upgrading to advanced capsule fillers has been crucial for my pharmacy. I’ve observed that these machines not only boost the output significantly but also maintain a high standard of quality, which is non-negotiable in our field. The shift from manual to automated processes has streamlined our operations, allowing us to produce larger batches within shorter timeframes without compromising the accuracy of dosages.
This newfound efficiency has empowered me to meet patient demands more effectively. With increased production capabilities, I can confidently address fluctuations in orders while ensuring consistent quality across every capsule:
- Boost in output capacity allows for larger batch production.
- Enhanced quality control measures maintained through automation.
- Improved ability to respond to patient demand fluctuations.
Weighing Initial Costs Against Competitive Advantages Gained
Determining the initial investment for advanced capsule filling machines can be daunting; however, I find that the long-term competitive advantages far outweigh these initial costs. By enhancing our operational efficiency, I am able to increase production volumes and deliver higher-quality products, which positions my pharmacy more favorably in the marketplace. This strategic investment not only improves our bottom line but also reinforces our reputation for reliability among our customers.
The interplay between upfront costs and the resulting benefits is crucial for making informed decisions. It’s about more than just the financial metrics; it’s about what these machines enable me to achieve over time. I can anticipate growth in demand and adapt quickly, ensuring my pharmacy remains competitive:
- Investing in technology enhances production efficiency.
- Higher output leads to improved market positioning.
- Stronger reputation fosters customer loyalty.
Upgrading to advanced capsule fillers can significantly enhance operational efficiency and reduce costs for pharmacies. Now, let’s look at real-world examples that showcase the successful implementation of these automatic filling systems and the impressive results they’ve achieved.
Case Studies: Successful Implementations of Automatic Filling Systems
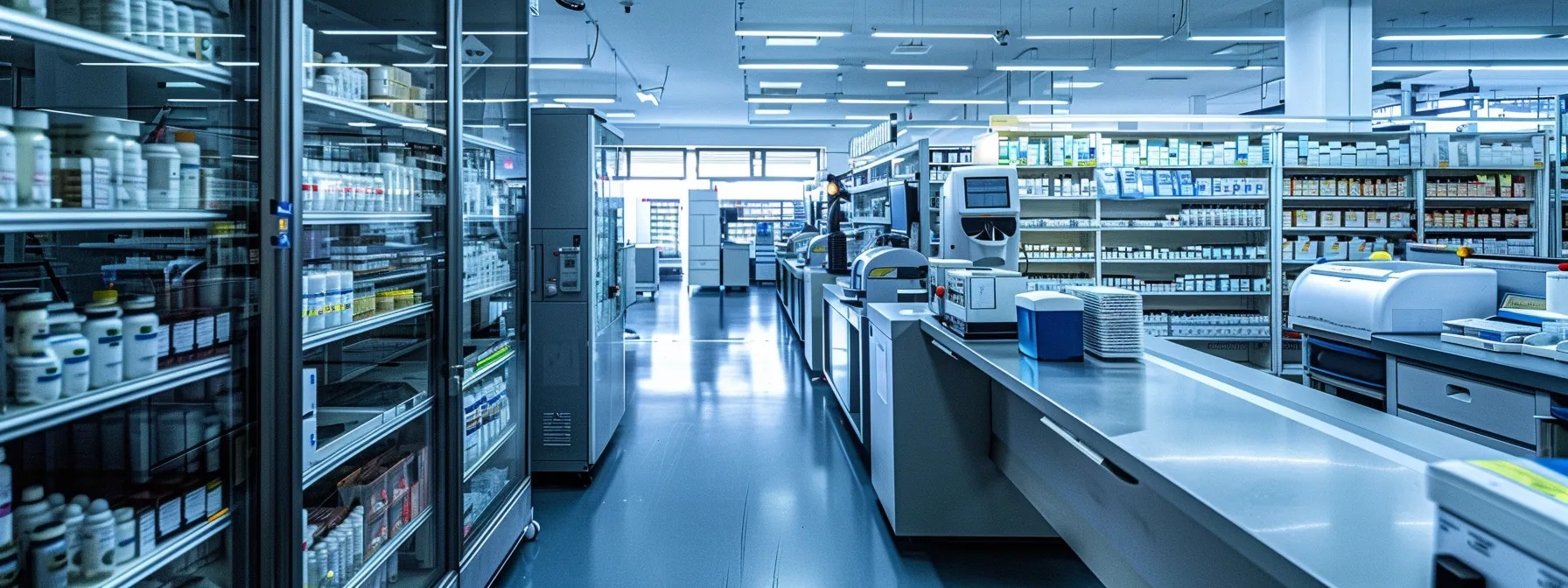
Through my experiences, I’ve observed that the implementation of automatic capsule filling systems varies greatly among pharmacies of different sizes and operational focuses. For small pharmacies, compact machines provide strategic solutions that allow for scaling production without excessive space requirements. In contrast, larger operations benefit from high-capacity fillers designed for mass production, streamlining their output significantly. Custom solutions emerge as essential for specialized pharmaceutical needs, ensuring that unique formulations are handled with precision. On a broader scale, global pharmaceutical giants leverage automation not just for efficiency, but for seamless worldwide distribution and responsiveness to market demands. Each case illustrates how tailored technology can drive operational success across diverse pharmacy landscapes.
Small Pharmacy Solutions: Scaling Production With Compact Machines
In my experience with small pharmacies, integrating compact automatic capsule filling machines has proven invaluable for scaling production effectively. These machines are designed to occupy minimal space while delivering impressive output rates, allowing us to enhance our operational capabilities without overwhelming our facility. By investing in these compact solutions, I’ve streamlined processes significantly, ensuring we can respond efficiently to patient needs while maintaining quality standards.
Utilizing compact machines has also empowered my pharmacy to be more agile in addressing fluctuating demands. For instance, when seasonal prescription volumes rise, these systems allow us to increase production without extensive downtime or the need for large-scale operational changes. This adaptability plays a crucial role in ensuring that we remain competitive and responsive to our community’s requirements:
- Small pharmacies leverage compact machines for efficient scaling.
- Minimal space usage combined with high output rates enhances operations.
- Agility in production helps meet fluctuating demands effectively.
Large-Scale Success: Implementing High-Capacity Fillers for Mass Production
In my experience working with larger pharmaceutical operations, I have witnessed the remarkable impact of high-capacity automatic capsule filling machines on productivity. These systems streamline the entire production process, allowing us to produce thousands of capsules per hour, which effectively meets the demands of large-scale distribution. By implementing these machines, my team has been able to maintain consistency in quality while significantly reducing production timelines, making us more competitive in the market.
As I reflect on how these high-capacity fillers were integrated into our workflow, several key advantages stand out:
- Enhanced production speed without sacrificing quality.
- Ability to handle larger batch sizes seamlessly.
- Improved operational efficiency leading to cost savings.
Custom Solutions: Tailoring Equipment for Specialized Pharmaceutical Needs
In my pursuit of efficiency and accuracy, I’ve found that customizing equipment for specialized pharmaceutical needs can significantly elevate our operational capabilities. For example, when introducing a unique line of herbal capsules, I collaborated with manufacturers to develop systems that accommodate the specific density and composition of these formulations. This tailored approach not only enhanced filling accuracy but also minimized waste, ensuring that we deliver the most effective products to our patients.
Moreover, I’ve employed bespoke solutions that allow for easy adaptability to changing formulations without disrupting workflow. By integrating flexible filling systems, I can quickly adjust parameters to accommodate new product lines, ensuring we remain agile in a competitive market. This adaptability has been crucial in addressing specific patient requirements, reinforcing my commitment to providing top-quality pharmaceutical care tailored to our community’s needs.
Global Pharmaceutical Giants: Leveraging Automation for Worldwide Distribution
In my experience working with global pharmaceutical giants, the integration of automatic capsule filling machines plays a pivotal role in optimizing their distribution networks. These sophisticated systems enable companies to maintain high throughput rates while ensuring the consistency and reliability of their products, which is crucial for meeting international regulatory standards. This level of efficiency allows for the seamless distribution of medications across various regions, ensuring that patients receive their prescriptions in a timely manner.
Furthermore, the utilization of automation allows these large-scale operations to forecast demand accurately and respond to market fluctuations without compromising on quality. Companies can swiftly adapt production lines to accommodate varying batch sizes, enhancing their agility in addressing customer needs globally. This adaptability is essential for maintaining a competitive edge and allows for a rapid response to emerging trends in healthcare:
- High throughput rates ensure timely distribution.
- Consistency and reliability meet international standards.
- Accurate demand forecasting enhances operational agility.
- Swift adaptation to market fluctuations reinforces competitiveness.
Conclusion
Automatic capsule filling machines significantly enhance the efficiency and precision of pharmaceutical operations. By streamlining production processes and reducing human error, these machines ensure consistent medication dosages that meet stringent quality standards. They offer scalability, allowing pharmacies to adapt to fluctuating demands without compromising quality. Ultimately, integrating this technology positions pharmacies to deliver superior care while maintaining a competitive edge in the industry.
Share This Story, Choose Your Platform!
Get In Touch
Phone: (847) 722-6942
Email: sales@end2endlogix.com
Web: end2endlogix.com