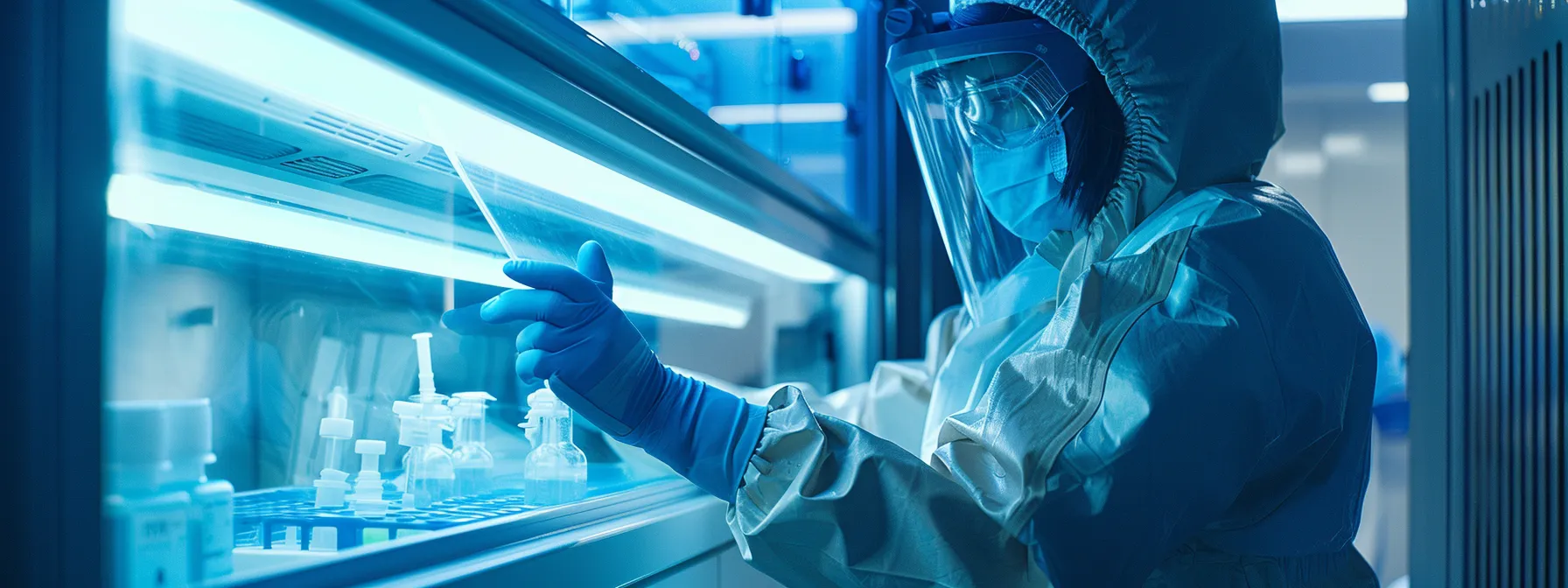
Are you confident that your compounding pharmacy equipment is operating at peak performance? Regular maintenance is not just important for efficiency; it’s essential for patient safety and regulatory compliance. In this article, I will discuss key strategies such as establishing a preventative maintenance schedule, daily inspection routines, and training staff on equipment care. By implementing these practices, you can address potential issues, ensure ingredient integrity, and reduce downtime, ultimately enhancing your pharmacy’s overall effectiveness and reliability.
Key Takeaways
- Regular maintenance prevents equipment failures, ensuring operational efficiency and consistency in medication quality
- Cleanliness of compounding equipment is vital for preventing contamination, especially in sensitive preparations
- Adherence to regulatory standards protects pharmacies from penalties and reinforces patient safety
- Staff training on equipment use enhances safety and reliability in compounding processes
- Establishing communication protocols boosts team preparedness during emergencies, ensuring swift responses to equipment issues
Understanding the Importance of Regular Maintenance
Regular maintenance of compounding pharmacy equipment is crucial for several reasons. It helps prevent equipment failure and unnecessary downtime that could halt operations, impacting accuracy and quality in compounding. By ensuring effective calibration and integrity of the equipment, we also guarantee compliance with regulatory standards. Furthermore, routine checks can extend the lifespan of equipment while enhancing safety within the pharmacy, reducing the risk of adverse effects on both staff and patients.
Prevent Equipment Failure and Downtime
Preventing equipment failure and downtime is vital for maintaining the operational efficiency of our compounding pharmacy. Regular maintenance checks for equipment dedicated to compounding drugs ensure that we can promptly address any signs of wear and tear. This proactive approach not only protects our investment but also upholds the high standards of quality control that our patients deserve.
In my experience, one area that often gets overlooked is the cleanliness of compounding equipment, especially in chemotherapy preparations, where even minute impurities can lead to severe consequences. By establishing a routine maintenance schedule that includes cleaning and calibrating our machinery, we can significantly reduce the risk of downtime. An effective maintenance strategy helps us consistently deliver safe and high-quality medications to our patients:
- Regular inspections to identify potential issues.
- Scheduled cleaning of equipment to prevent contamination.
- Calibration checks to ensure accuracy in drug compounding.
Maintain Compounding Accuracy and Quality
Maintaining compounding accuracy and quality is essential to meet the standards set by the Food and Drug Administration (FDA). Accurate dosing is critical, especially in compounding sterile preparations. Any deviation or contamination during the compounding process can lead to severe health risks for patients, which underscores the importance of strict adherence to quality assurance protocols.
Through my experience, I have learned that implementing routine maintenance checks and calibration procedures significantly enhances the safety and efficacy of our medications. By regularly assessing our compounding equipment, we can ensure precise measurements and reduce the likelihood of contamination, ultimately delivering medications that are both safe and effective. This commitment to maintenance not only protects our patients but also reinforces trust in our pharmacy’s ability to provide high-quality pharmaceutical care.
Ensure Regulatory Compliance
In my role, I have found that adherence to regulatory standards is non-negotiable for compounding pharmacies. Regular inspections of equipment not only ensure that we meet the strict guidelines set by health authorities but also protect our operations from costly penalties. By maintaining rigorous maintenance schedules, I can confidently confirm that our equipment operates optimally, reducing the chances of issues that could compromise patient safety.
One specific area I focus on is managing dust accumulation and pressure within compounding equipment. Even the smallest debris can lead to contamination, so routine checks are essential. By proactively addressing these concerns, I create a safer environment for both staff and patients, reinforcing our commitment to quality in health care. This dedication to regular maintenance has proven invaluable in sustaining our pharmacy’s reputation as a trusted provider of compounded medications.
Extend Equipment Lifespan
Extending the lifespan of compounding pharmacy equipment is a crucial aspect of our operational strategy. By implementing predictive maintenance techniques, we can anticipate potential failures before they occur, ensuring that our systems operate efficiently. This proactive approach not only allows us to maintain a full formulary of preparations but also ensures that sterile compounding processes remain uninterrupted, which is vital for patient safety.
In my practice, I prioritize regular maintenance checks that focus on equipment used for specialized preparations, such as those prescribed by physicians for patients with specific needs. By addressing wear and tear early, we significantly reduce the risk of costly equipment replacements and maintain the high-quality standards necessary for effective sterile compounding. This commitment to care not only prolongs the life of our equipment but also reinforces our dedication to providing reliable pharmaceutical services.
Enhance Safety in the Pharmacy
Enhancing safety in the pharmacy starts with strict adherence to hygiene protocols and maintaining compliance with relevant laws. I have seen firsthand how routine audits of our compounding equipment can identify potential hazards that may compromise the cleanliness and safety of our work environment. Implementing regular sterilization procedures and cleaning schedules not only protects our team but also reassures patients about the integrity of the medications they receive.
In my experience, focusing on the sanitation of compounding areas and machinery significantly reduces the risk of contamination. This commitment to thorough maintenance ensures that our manufacturing processes remain compliant with health regulations, ultimately safeguarding our patients’ health. Creating a culture of safety and hygiene in our pharmacy strengthens trust with our clients, knowing that we prioritize their well-being above all else.
Regular maintenance protects your investment and keeps operations running smoothly. Now, let’s look at how to create a practical preventative maintenance schedule to ensure long-term success.
Establishing a Preventative Maintenance Schedule
Establishing a preventative maintenance schedule is essential for effective equipment maintenance in compounding pharmacies. I focus on identifying critical equipment and components, creating a detailed maintenance calendar, and assigning responsibilities to team members. Keeping accurate maintenance records and utilizing maintenance management tools enhances workflow and ensures compliance with international organization for standardization (ISO) standards. These strategies will directly impact airflow management and the drug delivery process, ultimately safeguarding patient safety.
Identify Critical Equipment and Components
Identifying critical equipment and components in a compounding pharmacy is essential for ensuring patient safety and compliance with regulatory standards. I focus on evaluating essential machinery such as laminar flow hoods, compounders, and sterilizers in the cleanroom environment. These pieces of equipment are pivotal in minimizing toxicity and preventing contamination, which can pose significant risks to patients.
Evaluating components like air filtration systems and waste containment units is equally important. By acknowledging their role in maintaining a sterile environment, I can effectively reduce the potential for hazardous waste and ensure that our compounding processes uphold the highest standards of safety. This careful consideration allows us to maintain operational efficiency while protecting both staff and patients from unnecessary risks.
Create a Maintenance Calendar
Creating a maintenance calendar is a practical approach that helps streamline our compounding pharmacy’s operations. By scheduling regular cleaning of equipment with appropriate disinfectants, I ensure that all dosage forms are prepared in safe environments. This proactive planning also helps to align our practices with the latest pharmacopoeia standards, promoting patient safety and medication efficacy.
To effectively implement this maintenance calendar, I prioritize key tasks based on the route of administration and the specific needs of our medications. By categorizing maintenance activities—such as calibration of compounding machinery and sterilization of tools—I can clearly outline responsibilities for team members. This organized system not only enhances our compliance checks but also ensures we remain focused on delivering high-quality compounded medications:
- Regular cleaning with appropriate disinfectants.
- Scheduled calibration and maintenance of compounding equipment.
- Documentation to comply with pharmacopoeia standards.
- Assigning responsibilities based on medication route of administration.
Assign Responsibilities to Team Members
Assigning responsibilities to team members is a critical step in ensuring that our preventative maintenance schedule for compounding pharmacy equipment is effective. I make it a priority to designate specific roles to each team member based on their expertise and experience with medical equipment, such as barrier isolators and sterile compounding devices. This clear division of tasks not only enhances accountability but also aligns with federal law and the standards set by the United States Pharmacopeia (USP) for maintaining equipment integrity and safety.
To ensure comprehensive cover for all aspects of maintenance, I implement a collaborative approach where each team member is responsible for familiarizing themselves with the equipment they oversee. For instance, I have seen how assigning a staff member to monitor the calibration of our compounded drug machinery can prevent potential deviations from established protocols. By creating a culture where everyone understands their role in the maintenance process, we not only improve compliance with regulations but also foster a team that prioritizes patient safety and medication efficacy:
- Designate roles based on expertise with medical equipment.
- Ensure accountability through clear task assignments.
- Foster a culture of understanding and compliance among the team.
Keep Detailed Maintenance Records
Keeping detailed maintenance records is a fundamental aspect of our preventative maintenance strategy for pharmacy equipment. By documenting every maintenance activity, from routine inspections to calibration of machines, I can effectively monitor the lifespan and performance of our equipment. This practice not only reduces the risk of equipment failure but also ensures compliance with regulatory standards, thereby safeguarding patient health.
In my role, I can see how thorough records serve as a valuable reference point for future maintenance schedules, aiding in the identification of trends or recurring issues. When I can quickly access the maintenance history of personal protective equipment or compounding machinery, it allows me to anticipate potential risks and address them proactively. For pharmacies seeking to improve their operational efficiency, I recommend implementing a robust record-keeping system. If you have questions or need assistance, feel free to Contact Us at End2End Logix to explore tailored solutions for your pharmacy’s needs.
Utilize Maintenance Management Tools
Utilizing maintenance management tools has become an integral part of my strategy for ensuring the reliability of Hospital Equipment in our compounding pharmacy. These tools, such as computerized maintenance management systems (CMMS), allow me to schedule, track, and document maintenance activities effectively. By keeping everything organized in one place, I can quickly access information about previous maintenance checks and upcoming tasks, which helps prevent unexpected equipment failures.
Additionally, maintenance management tools streamline communication within our pharmacy team, ensuring that everyone is aware of their responsibilities. For instance, I have implemented alerts and notifications for routine maintenance checks, which has significantly improved compliance with our schedule and reduced downtime. This proactive approach not only enhances the efficiency of our operations but also contributes to the overall safety and quality of the compounding processes.
- Implement computerized maintenance management systems (CMMS).
- Schedule, track, and document maintenance activities effectively.
- Access previous maintenance checks and upcoming tasks easily.
- Streamline communication and enhance team awareness of responsibilities.
- Set up alerts and notifications for routine maintenance checks.
With a solid maintenance schedule in place, the focus now turns to the daily tasks that keep everything running smoothly. Regular inspection and cleaning are essential; they prevent small problems from becoming big ones.
Daily Inspection and Cleaning Procedures
Conducting daily inspections and cleaning procedures is pivotal for maintaining the reliability of compounding pharmacy equipment. I focus on performing visual checks for wear and damage, ensuring equipment functions properly. I clean equipment using established techniques, apply sanitization protocols to prevent contamination, and follow handling and storage guidelines. Additionally, I prioritize safe waste disposal to uphold safety standards in our pharmacy.
Conduct Visual Checks for Wear and Damage
Conducting visual checks for wear and damage is a fundamental part of my daily inspection routine for compounding pharmacy equipment. Each morning, I thoroughly examine critical components like laminar flow hoods and compounders, looking for signs of wear, cracks, or any irregularities that could affect performance. This proactive approach not only helps me identify potential issues early but also reinforces our commitment to maintaining the highest standards of safety and efficacy in our medications.
In my practice, I’ve found that documenting any visible damage immediately allows us to address concerns before they escalate into significant problems. By noting down the condition of equipment components during these inspections, I ensure our maintenance procedures are informed and timely. This routine not only keeps our operations running smoothly but also instills confidence in our team and patients, knowing that we prioritize safety and reliability in our compounding processes.
Clean Equipment Following Proper Techniques
Cleaning compounding pharmacy equipment requires adherence to established protocols to ensure it operates effectively and maintains safety standards. I focus on using appropriate disinfectants that are compatible with the materials of the equipment, as improper cleaning agents can lead to damage or contamination. Regular cleaning not only eliminates potential contaminants but also reinforces our commitment to quality in medication preparation.
Following proper techniques for cleaning helps create a sterile environment, which is crucial for patient safety, especially in sensitive compounding processes. I ensure that all team members are trained on the correct procedures, including the use of protective equipment and the correct application of cleaning solutions. This structured approach guarantees that we consistently uphold the highest hygiene standards, mitigating risks associated with contamination:
- Use appropriate disinfectants for equipment materials.
- Train staff on cleaning procedures and safety measures.
- Regularly review and update cleaning protocols as needed.
Apply Sanitization Protocols to Avoid Contamination
Applying sanitization protocols is a crucial step in maintaining a contamination-free environment within our compounding pharmacy. I ensure that every team member is trained to follow strict sanitization guidelines, including using appropriate disinfectants and adhering to scheduled cleaning practices. These protocols not only protect the integrity of our compounded medications but also contribute to the overall safety of our work area.
To effectively implement these sanitization protocols, I focus on high-touch areas and frequently used equipment, such as laminar flow hoods and other compounding devices. By incorporating a routine that addresses all potential contamination points, I minimize the risk of harmful substances entering our preparations. These strategies enhance our commitment to delivering safe and effective medications to our patients, ensuring that we maintain the trust and safety of everyone who relies on our pharmacy:
- Train staff on proper sanitization techniques.
- Use compatible disinfectants for all equipment.
- Regularly review and follow cleaning schedules.
- Focus on high-touch areas and frequently used equipment.
Adhere to Handling and Storage Guidelines
Adhering to proper handling and storage guidelines is paramount for ensuring the integrity of compound pharmacy equipment. Every piece of equipment, from laminar flow hoods to compounding devices, must be stored under controlled conditions that prevent exposure to extreme temperatures or moisture, which can lead to performance issues. In my experience, I always ensure that equipment is not overcrowded in storage areas, allowing for adequate airflow and minimizing the risk of accidental damage during retrieval or use.
Furthermore, it’s crucial to follow specified procedures for handling equipment to avoid contamination and maintain sterility. Each team member is trained to use protective gear and to handle machinery carefully to prevent any adverse effects. By implementing these best practices in handling and storage, I protect our equipment and ultimately contribute to the safety and quality of the compounded medications we provide, reinforcing our commitment to high standards in pharmaceutical care.
Dispose of Waste Safely and Responsibly
Disposing of waste safely and responsibly is a critical component of daily procedures in a compounding pharmacy. In my practice, I ensure that all hazardous waste is segregated and disposed of according to regulatory guidelines. This not only protects our environment but also safeguards the health and safety of our staff and patients by minimizing exposure to potentially harmful substances.
I’ve found that implementing proper disposal protocols for waste materials, such as unused drugs and contamination byproducts, is essential for maintaining a compliant and efficient pharmacy. By training my team on the importance of waste disposal practices, I create a culture of responsibility that reinforces our commitment to safety standards. This proactive approach minimizes risks and ensures that we deliver high-quality compounded medications to our patients without compromise.
Keeping equipment in top shape is just the beginning. It’s equally vital to train staff on how to use and care for it, ensuring that each tool serves its purpose with precision.
Training Staff on Equipment Use and Care
Training Staff on Equipment Use and Care
Providing comprehensive training sessions is essential for ensuring that all pharmacy staff are skilled in proper equipment use and care. I develop clear standard operating procedures and encourage open communication for reporting any concerns. Investing in continuing education opportunities fosters a culture of safety and accountability, empowering our team to maintain high standards in compounding practices.
Provide Comprehensive Training Sessions
Providing comprehensive training sessions is vital for my pharmacy staff to ensure they are proficient in operating and maintaining compounding pharmacy equipment. I develop tailored training programs that cover all aspects of equipment use, focusing on safety protocols and best practices. This hands-on training not only enhances their skills but also empowers them to identify potential issues early, ultimately preserving the integrity of our compounding processes.
I incorporate practical examples and real-life scenarios into the training, making the content relatable and applicable for the team. By encouraging open communication, staff can comfortably report concerns and share experiences regarding equipment performance. This collective knowledge fosters a culture of continuous learning and accountability, which is essential for maintaining high standards in compounding pharmacy operations:
- Hands-on training on equipment operation and safety protocols.
- Utilizing real-life scenarios to enhance learning and application.
- Encouraging open communication for reporting concerns and sharing insights.
Develop Clear Standard Operating Procedures
Developing clear standard operating procedures (SOPs) is fundamental to ensuring that all pharmacy staff understand the proper use and care of compounding pharmacy equipment. I focus on creating comprehensive SOPs that outline every aspect of equipment handling, maintenance tasks, and safety protocols. This structured approach not only enhances operational efficiency but also helps mitigate risks associated with improper equipment use, ultimately safeguarding both our patients and our practice.
In my experience, involving team members in the development of these procedures fosters a sense of ownership and accountability. I regularly conduct training sessions that break down the SOPs into manageable segments, allowing staff to gain confidence in their roles. By providing practical examples and interactive discussions, I ensure that my team is well-equipped to adhere to these standards, which are vital for maintaining the integrity of our compounding processes and enhancing overall patient safety.
Encourage Open Communication and Reporting
Encouraging open communication among staff is vital in ensuring effective training and maintenance of compounding pharmacy equipment. I prioritize creating an environment where team members feel comfortable sharing their observations and concerns regarding equipment performance. When staff can report issues early, we can address potential problems before they escalate, maintaining high operational standards and the safety of our compounded medications.
I implement regular team meetings and check-ins to foster dialogue about equipment use and care. In these discussions, I emphasize the importance of sharing experiences and insights related to equipment operations. By cultivating a culture of transparency and accountability, we not only enhance our maintenance strategies but also empower our team to take ownership of their roles in safeguarding patient safety and medication quality:
- Encourage team members to share equipment observations.
- Conduct regular meetings to discuss equipment performance.
- Foster accountability and ownership in equipment maintenance.
Invest in Continuing Education Opportunities
Investing in continuing education opportunities is essential for keeping my pharmacy staff up-to-date on the latest practices and technologies in compounding pharmacy equipment. By providing access to workshops, webinars, and certification programs, I empower team members to enhance their skills and address any gaps in knowledge. This ongoing training not only ensures compliance with industry standards but also promotes a culture of continuous improvement within our pharmacy.
In my experience, regular training sessions have proven invaluable for enhancing equipment usage and care. For example, when I organized a workshop on proper sterilization techniques, the staff reported a noticeable increase in their confidence and efficiency. With well-trained team members, I can maintain high-quality standards in our compounding processes, ultimately ensuring patient safety and satisfaction:
- Provide access to workshops and webinars.
- Encourage participation in certification programs.
- Promote a culture of continuous improvement.
- Organize practical hands-on training sessions.
- Enhance staff confidence in equipment use and care.
Foster a Culture of Safety and Accountability
Fostering a culture of safety and accountability in my pharmacy is essential for effective equipment maintenance and optimal compounding practices. I encourage every team member to take ownership of their tasks, which includes reporting any equipment concerns or irregularities immediately. This open line of communication ensures that we can address potential issues before they escalate, ultimately protecting the quality of our compounded medications and enhancing patient safety.
To support this culture, I conduct regular training sessions that emphasize the importance of vigilance in equipment use. I share real-life scenarios and experiences that illustrate the consequences of minor oversights, fostering a sense of responsibility among the staff. By creating an environment where safety is prioritized and accountability is expected, I empower my team to maintain high standards and support our pharmacy’s mission to deliver reliable pharmaceutical care:
- Encourage team members to take ownership of their tasks.
- Foster immediate reporting of equipment concerns.
- Conduct training sessions emphasizing vigilance in equipment use.
- Create an environment prioritizing safety and accountability.
Training the staff was just the beginning. Now, we turn to those who make the equipment—a partnership that promises greater support and innovation.
Collaborating With Manufacturers and Service Providers
Collaborating With Manufacturers and Service Providers
To ensure optimal performance of our compounding pharmacy equipment, I focus on several key strategies. First, I adhere to manufacturer maintenance guidelines to guarantee compliance and efficiency. Scheduling regular professional servicing, sourcing genuine replacement parts, managing warranties and service agreements, and staying updated on equipment innovations all play vital roles in maintaining the integrity of our pharmacy operations. Each of these topics will be discussed in detail to provide practical insights that can enhance our maintenance practices.
Follow Manufacturer Maintenance Guidelines
Following manufacturer maintenance guidelines is essential for ensuring the longevity and efficiency of compounding pharmacy equipment. In my practice, I make it a priority to familiarize myself with the specific requirements outlined by manufacturers for each piece of equipment we use. This includes regular servicing and calibration checks as recommended, which not only helps maintain accuracy but also safeguards compliance with health regulations.
By adhering to these guidelines, I can prevent potential issues that arise from neglect or improper maintenance. For instance, after consistently applying the manufacturer’s recommendations for my laminar flow hood, I noticed a significant reduction in equipment malfunctions. This proactive approach not only enhances the reliability of our compounding processes but also reinforces our commitment to delivering safe and high-quality medications to our patients.
Schedule Regular Professional Servicing
Scheduling regular professional servicing for compounding pharmacy equipment is an essential practice that I have found to significantly enhance operational efficiency. By collaborating with equipment manufacturers, I ensure that all servicing aligns with their specific recommendations, which helps maintain the equipment‘s performance and longevity. These regular checks not only prevent potential issues but also address any concerns early on, safeguarding compliance with health regulations and the quality of our compounded medications.
In my experience, working closely with service providers who specialize in compounding pharmacy equipment allows me to stay informed about any necessary updates or repairs. During these servicing appointments, skilled technicians often provide insights into equipment functionality, helping us optimize usage and identify any adjustments needed for safety and efficacy. By prioritizing regular professional servicing, I strengthen our commitment to quality care, ensuring that our medications meet the rigorous standards expected in the pharmacy industry.
Source Genuine Replacement Parts
Sourcing genuine replacement parts for compounding pharmacy equipment is crucial for maintaining optimal performance and compliance with safety standards. In my experience, using authentic components significantly minimizes the risk of equipment malfunctions and ensures that systems operate as intended. By collaborating closely with manufacturers, I ensure that I obtain parts that meet the specified quality standards, which is essential for the reliability of our compounding processes.
Whenever I face issues that require replacements, I prioritize genuine parts because they not only enhance equipment longevity but also protect our pharmacy’s reputation for delivering safe medications. I have found that investing time in establishing strong relationships with manufacturers allows me to stay informed about the latest available parts and innovations in the market. This proactive approach protects our operations from unexpected downtimes caused by inferior or incompatible components, ultimately safeguarding the health and safety of our patients.
Manage Warranties and Service Agreements
Managing warranties and service agreements for our compounding pharmacy equipment is critical to maintaining operational efficiency. I make it a point to closely review the terms of our warranties, ensuring I fully understand the coverage offered by manufacturers. This knowledge allows me to take advantage of any available services without incurring additional costs, ultimately supporting the longevity and reliability of our equipment.
Additionally, I prioritize establishing strong relationships with service providers to manage these agreements effectively. By keeping a log of service agreements and warranty expiration dates, I can schedule timely maintenance and address potential issues before they escalate. This proactive approach not only protects our investment in equipment but also helps maintain compliance with health regulations, ensuring we are always prepared to deliver high-quality compounded medications:
- Regularly review warranty terms and conditions.
- Establish relationships with service providers for timely support.
- Keep track of service agreements and warranty dates.
- Schedule maintenance before warranty expiration to avoid lapses.
- Utilize warranty services to minimize repair costs.
Stay Updated on Equipment Innovations
Staying updated on equipment innovations is essential for maintaining the efficiency and safety of our compounding pharmacy. I make it a priority to attend industry conferences and subscribe to relevant publications that spotlight advancements in compounding technology. By doing so, I am equipped with the latest information on best practices and emerging technologies that can improve our operations and enhance patient care.
Additionally, I collaborate closely with manufacturers to gain insights into upcoming equipment updates and new features that could benefit our pharmacy. Understanding these innovations allows me to assess how they might enhance our compounding processes, reduce downtime, and ensure compliance with changing regulations. This proactive approach ultimately strengthens our pharmacy’s capabilities and reinforces our commitment to high-quality pharmaceutical care:
- Attend industry conferences and engage in professional development.
- Subscribe to industry publications for the latest trends.
- Collaborate with manufacturers to learn about new technologies.
- Assess the benefits of innovations for operational efficiency.
Even the best equipment can fail when least expected. It’s wise to prepare for emergencies to safeguard what matters most.
Preparing for Emergency Situations
To effectively prepare for emergency situations involving compounding pharmacy equipment, I focus on several key strategies. First, I create contingency plans for potential equipment failure, ensuring our operations can continue smoothly. I also maintain backup equipment and supplies to minimize disruptions, establish rapid repair procedures to swiftly address issues, and implement effective communication protocols. Regularly reviewing and improving our emergency plans allows us to adapt and enhance our preparedness, ultimately safeguarding patient care and operational efficiency.
Create Contingency Plans for Equipment Failure
Creating contingency plans for equipment failure is essential in compounding pharmacies to ensure that operations can continue without interruption. In my experience, it is crucial to identify key equipment that, if compromised, could halt compounding processes. By establishing clear protocols for both immediate response and alternative workflows, I can mitigate potential disruptions, ensuring that patient care remains a priority even during unexpected situations.
Moreover, I recommend regularly testing these contingency plans through simulations that replicate potential equipment failures. This practice not only familiarizes the staff with the emergency procedures but also highlights any gaps in our response strategies. By maintaining well-documented contingency plans, I ensure that my team is prepared and confident in handling equipment issues, minimizing downtime and reinforcing our commitment to delivering safe and reliable compounded medications.
Maintain Backup Equipment and Supplies
Maintaining backup equipment and supplies is a critical component of our emergency preparedness in the compounding pharmacy. I prioritize having essential backup devices, such as additional laminar flow hoods or compounding machines, ready for immediate use in case of equipment failure. This practice minimizes disruptions in our workflows, ensuring that patient care remains uninterrupted, even when unexpected challenges arise.
In addition to backup devices, I ensure that we have a well-stocked inventory of supplies, including essential chemicals and compounding materials. By keeping these items readily available, I can quickly switch to alternate workflows when necessary, safeguarding our operations against downtime. Proper inventory management allows us to respond swiftly to any equipment issues, reinforcing our commitment to providing safe and effective compounded medications to our patients:
- Identify critical equipment for backup readiness.
- Keep an updated inventory of essential supplies.
- Establish procedures for swift switching to backup systems.
- Regularly test and assess the reliability of backup equipment.
Establish Rapid Repair Procedures
Establishing rapid repair procedures is essential for maintaining the functionality of compounding pharmacy equipment during emergencies. I prioritize creating a straightforward process that enables my team to quickly assess equipment failures and implement immediate solutions. This ensures that any disruptions in our compounding operations are minimized, allowing us to uphold patient safety and medication quality.
To facilitate effective repairs, I maintain a readily accessible inventory of critical spare parts and establish relationships with local service technicians. This proactive approach enables us to reduce downtime and address issues swiftly, protecting our pharmacy’s operations from potential setbacks. By regularly reviewing and updating these repair procedures, I ensure that our processes remain effective and responsive in high-pressure situations:
- Identify critical equipment for repair procedures.
- Keep an inventory of essential spare parts.
- Establish connections with service technicians for timely support.
- Regularly test and update repair strategies to ensure effectiveness.
Implement Effective Communication Protocols
Implementing effective communication protocols is vital for ensuring that all staff are informed and prepared during emergency situations involving compounding pharmacy equipment. I have found that establishing clear lines of communication helps eliminate confusion and ensures that everyone knows their roles in times of need. For example, my team regularly conducts drills that simulate equipment failures, allowing us to practice our emergency response and identify any improvements needed in our communication strategies.
In my experience, utilizing communication tools such as group messaging apps and regular team meetings enhances our ability to respond swiftly during a crisis. These platforms allow team members to quickly share important updates about equipment functionality and immediate action steps required during emergencies. By fostering a culture of open communication and proactive problem-solving, we can mitigate risks and enhance our pharmacy’s operational resilience:
- Establish clear lines of communication.
- Conduct simulation drills for emergency preparedness.
- Utilize communication tools to share updates quickly.
- Foster a culture of open communication.
- Enhance operational resilience through proactive problem-solving.
Review and Improve Emergency Plans Regularly
In my experience, regularly reviewing and improving our emergency plans is essential for maintaining the responsiveness and effectiveness of our compounding pharmacy. I advocate for conducting scheduled assessments of our emergency procedures, ensuring that they align with current equipment capabilities and regulatory standards. This practice not only keeps the plan relevant but also empowers our team to stay prepared for any equipment failures or unforeseen incidents that could disrupt operations.
I find that engaging staff during these reviews encourages valuable feedback and insights on potential gaps in our plans. By incorporating their perspectives, we create a culture of safety and readiness that enhances our overall operational resilience. Furthermore, conducting periodic drills to simulate emergency situations reinforces our preparedness, ensuring that everyone knows their role and can act swiftly when needed, ultimately safeguarding the quality of our compounded medications.
Conclusion
Essential maintenance strategies for compounding pharmacy equipment are critical to ensuring operational efficiency, compliance, and patient safety. By implementing routine maintenance, establishing a preventative schedule, and training staff effectively, pharmacies can significantly reduce equipment failures and enhance medication quality. Prioritizing hygiene, adhering to manufacturer guidelines, and fostering a culture of accountability not only protect the integrity of compounded medications but also uphold the pharmacy’s reputation. Investing in these strategies ultimately safeguards patient health and reinforces the commitment to delivering high-quality pharmaceutical care.
Share This Story, Choose Your Platform!
Get In Touch
Phone: (847) 722-6942
Email: sales@end2endlogix.com
Web: end2endlogix.com