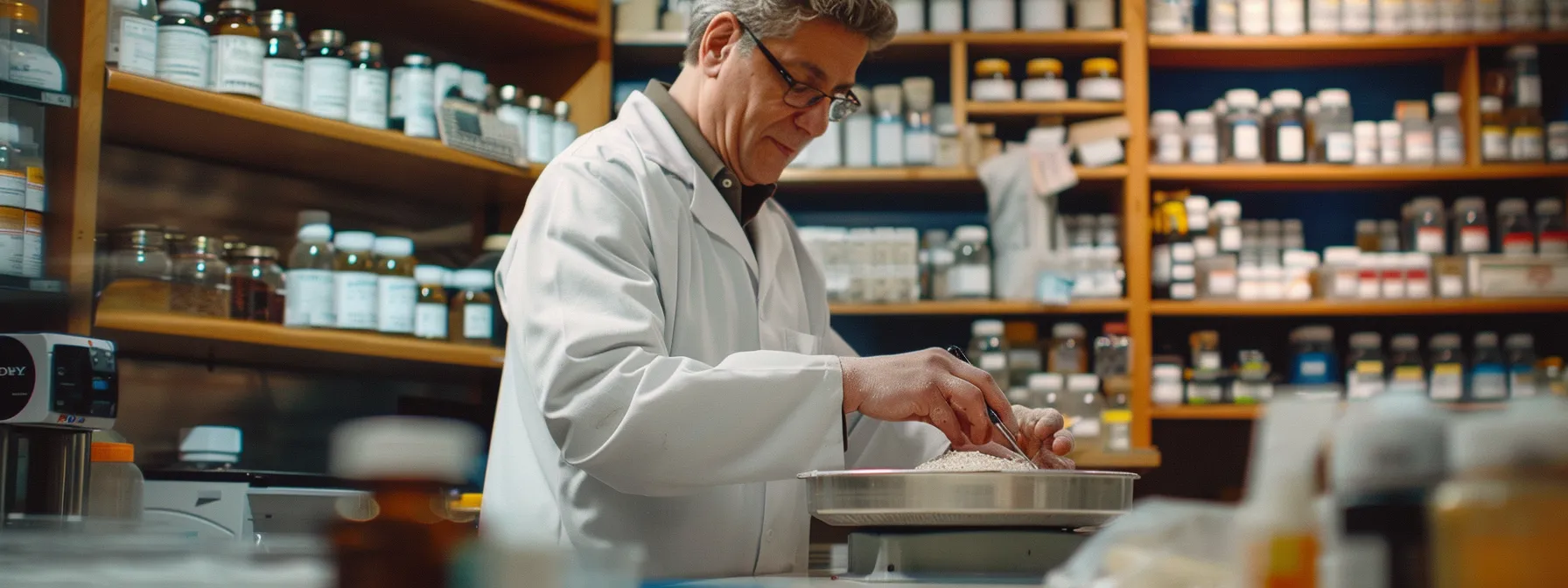
In the world of pharmacy compounding, having the right tools and equipment is essential for success. Did you know that proper calibration and the use of specialized equipment can enhance occupational safety and health while ensuring compliance with Food and Drug Administration guidelines? In this comprehensive guide, I will cover essential compounding tools, advanced equipment for specialized dosage forms, and the safety equipment you need to operate efficiently. By engaging with this content, you’ll gain insights into improving your compounding practice, addressing pain points like equipment selection and compliance challenges. Let’s dive in!
Key Takeaways
- proper compounding tools enhance safety and efficiency in medication preparation
- regular maintenance of equipment ensures compliance and patient safety
- automation in compounding processes reduces human error and improves operational efficiency
- eco-friendly practices contribute to sustainability and operational cost reduction
- adapting to regulatory changes is essential for maintaining high standards in pharmacy compounding
Essential Compounding Tools Every Pharmacy Needs
In my experience as a pharmacy consultant, having the right compounding tools is vital for safety and efficiency in medication preparation. Mortars and pestles, spatulas, and ointment slabs are essential for effective mixing, while precision balances ensure accurate weighing. Additionally, capsule filling machines simplify production, and graduated cylinders with beakers allow for precise measurements, making them indispensable in a laboratory setting.
Mortars and Pestles: Choosing the Right Material
Choosing the right material for mortars and pestles is crucial for effective medication compounding, particularly when working with hazardous drugs. I recommend ceramic or glass for non-reactive substances, as they provide a clean surface that minimizes the risk of contamination. Conversely, if your compounding tasks include more abrasive materials, such as certain drugs, a mortar and pestle made of porcelain or stone can be more effective due to their durability and excellent grinding capabilities.
Furthermore, consider the practicality of your tools in everyday manufacturing processes. Using a spatula made from non-porous material can enhance safety by preventing residue build-up during mixing. Effective contamination control is essential in compounding pharmacies, so ensuring that materials used in conjunction with mortars and pestles are compatible with the drugs being prepared will ensure a safer and more efficient workflow.
Spatulas and Ointment Slabs for Efficient Mixing
In my role as a pharmacy consultant, I’ve observed that spatulas and ointment slabs play a critical role in the compounding process within health care settings, particularly in hospital pharmacies. These tools not only facilitate efficient mixing of ingredients but also ensure compliance with formulary guidelines and legal standards. Using spatulas made of non-reactive materials can substantially reduce the risk of contamination, which is essential for maintaining safety and efficacy in medication preparation.
Ointment slabs, on the other hand, provide a dedicated space for compounding various topical formulations, optimizing the mixing process in a cleanroom environment. I recommend keeping multiple spatulas and slabs readily available to promote a streamlined workflow and prevent cross-contamination of substances. Adopting best practices with these tools ensures that your compounding operations meet regulatory requirements while upholding the highest quality standards:
- Ensure spatulas are made from non-porous materials for safety.
- Utilize ointment slabs for dedicated mixing of topical preparations.
- Maintain a cleanroom environment to prevent contamination.
- Adhere to formulary guidelines to guarantee medication accuracy.
Precision Balances for Accurate Weighing
Precision balances are integral to compounding pharmacies, as they ensure accurate weighing of ingredients necessary for formulating medications. According to the United States Pharmacopeia, maintaining compliance with quality assurance metrics is essential for patient safety and effective dosing. Additionally, using calibrated precision balances can help pharmacies minimize errors when measuring compounds that require exact dosages, especially when dealing with hazardous materials governed by the National Institute for Occupational Safety and Health guidelines.
In my experience, investing in high-quality precision balances can vastly improve operational efficiency. By utilizing these tools, pharmacies can confidently prepare medications that adhere to strict regulatory standards, safeguarding the health of patients. It’s vital for pharmacy managers to regularly check and calibrate these balances, as deviations in weight can compromise the integrity of the entire compounding process. With reliable weighing solutions, you can streamline the preparation of formulations, including those involving mortars and pestles, while ensuring each dose is accurately measured:
- Utilize precision balances to achieve accurate ingredient measurement.
- Calibrate balances regularly to maintain compliance.
- Adhere to United States Pharmacopeia standards for quality assurance.
- Follow National Institute for Occupational Safety and Health guidelines for hazardous materials.
Capsule Filling Machines to Streamline Production
Capsule filling machines significantly enhance the efficiency of compounding pharmacies by automating the process of filling capsules with precise formulations. In compliance with regulations from the National Association of Boards of Pharmacy, these machines ensure consistency in dosage, reducing the likelihood of human error during manual filling. Moreover, utilizing HEPA filters within these machines helps maintain a sterile environment, essential for safeguarding the integrity of the compounded medications and ensuring patient safety.
Additionally, integrating pumps into capsule filling machines streamlines the transfer of powders and liquids into capsules, increasing production speed. This is especially critical when medication expiration dates are a factor, as efficient production can help meet demanding timelines. By adopting these advanced tools, pharmacies can improve workflow, maintain quality control, and ultimately provide better service to their patients:
- Implement capsule filling machines for efficient medication production.
- Ensure compliance with National Association of Boards of Pharmacy regulations.
- Utilize HEPA filters for a sterile compounding environment.
- Incorporate pumps to expedite the filling process.
- Monitor expiration dates to guarantee drug safety.
Graduated Cylinders and Beakers for Precise Measurements
Graduated cylinders and beakers are crucial tools for ensuring precise measurements in pharmaceutical compounding. As I guide pharmacy technicians, I emphasize the importance of these instruments in maintaining asepsis and minimizing risk when preparing medications. Their design allows for accurate liquid measurement, essential for formulating compounds that comply with the Professional Compounding Centers of America standards, ultimately enhancing patient safety and quality control in the pharmaceutical industry.
In my experience, using graduated cylinders and beakers not only aids in achieving exact dosages but also supports a more organized workspace. I’ve seen firsthand how having these tools readily available can streamline processes and reduce the potential for errors, especially when working with multiple compounds. This is particularly important when a pharmacy technician is tasked with compounding complex formulations, as it reinforces adherence to proper procedures while protecting against contamination.
Every pharmacy needs the right tools to compound effectively. But for those looking to elevate their practice, advanced equipment opens new doors to precision and innovation.
Advanced Equipment for Specialized Compounding
In specialized compounding, advanced tools are essential for creating customized medications tailored to specific patient needs and routes of administration. High-speed homogenizers ensure uniform mixtures, while suppository molds facilitate the development of personalized dosage forms. Laminar flow hoods maintain sterile environments, electronic mortar and pestle systems enhance consistency, and automated compounding devices improve efficiency and quality control within the pharmacy.
High-Speed Homogenizers for Uniform Mixtures
In my experience, high-speed homogenizers are essential for achieving uniform mixtures in specialized compounding, particularly when formulating medications for chemotherapy patients. These machines effectively blend various components, ensuring that the final product adheres to the required standards for efficacy and safety. By utilizing high-speed homogenizers, pharmacies can enhance their workflow, reduce variability in dosages, and address the unique needs of patients requiring personalized medications.
When I recommend pharmacy equipment like high-speed homogenizers, I emphasize the importance of using personal protective equipment to safeguard technicians during the compounding process. This equipment not only promotes safety but also reinforces compliance with regulations set forth by overseeing bodies. Investing in high-speed homogenizers through suppliers like End2End Logix ensures that pharmacies can deliver consistent, high-quality formulations while optimizing their operational efficiency.
Suppository Molds for Customized Dosage Forms
In my work with pharmacies, I’ve found that suppository molds are invaluable for creating customized dosage forms tailored to patient needs. These molds allow for precise shaping and sizing, ensuring that each suppository delivers the correct dosage of active ingredients. This level of customization is particularly beneficial for patients who require specific formulations that may not be commercially available, providing a practical solution that enhances medication adherence and treatment efficacy.
When considering Hospital Equipment, it’s essential to select high-quality suppository molds that facilitate consistent production. Effective use of these molds can significantly streamline the compounding process, allowing pharmacies to respond quickly to patient prescriptions. If you’re looking to improve your compounding capabilities, I encourage you to reach out for expert guidance. Contact Us to explore our range of specialized compounding equipment that can enhance your pharmacy’s services.
Laminar Flow Hoods for Sterile Preparations
Laminar flow hoods are a crucial component in the compounding of sterile preparations, as they create a controlled environment that minimizes contamination. From my experience, using these hoods allows pharmacy technicians to work safely and efficiently while preparing medications that require a sterile environment. The consistent airflow ensures that the workspace remains free from airborne particles, which is vital in safeguarding patient health and ensuring the efficacy of compounded medications.
In my consultations with pharmacies, I stress the importance of properly utilizing laminar flow hoods. Regular maintenance and thorough cleaning are essential to uphold their effectiveness. I recommend setting clear protocols for the use of these hoods, including training staff on the correct procedures to prevent contamination. Following these guidelines can significantly enhance the quality of sterile preparations and ensure compliance with industry standards:
- Ensure laminar flow hoods are regularly maintained and cleaned.
- Train staff on proper usage and protocols to prevent contamination.
- Monitor airflow and filter conditions frequently for optimal performance.
Electronic Mortar and Pestle Systems
In my experience as a pharmacy consultant, electronic mortar and pestle systems significantly enhance the compounding process by providing consistent blending of compounds. These systems are designed to automate and streamline tasks, reducing the physical effort required from pharmacy technicians while increasing efficiency. I’ve seen how they help maintain uniformity in formulations, which is crucial for patient safety and compliance with industry standards.
Moreover, using electronic mortar and pestle systems minimizes the risk of human error that can occur with manual grinding. This added precision not only improves the quality of medications but also saves time, allowing team members to focus on other essential tasks in the pharmacy. Investing in this advanced equipment can lead to improved operational workflows and better outcomes for patient care, fulfilling the evolving needs of modern pharmacies.
Automated Compounding Devices for Efficiency
In my experience, automated compounding devices significantly enhance the operational efficiency of pharmacies. These machines streamline the compounding process by accurately measuring and mixing ingredients, which dramatically reduces the time required for medication preparation. They not only minimize human error but also increase the consistency of formulations, ensuring that every dose meets the required safety and efficacy standards.
Moreover, the integration of automated devices helps pharmacy teams manage workloads more effectively, particularly during peak hours. By automating repetitive tasks, such as mixing or filling, pharmacy staff can focus on critical aspects of patient care that require professional attention. This shift not only improves productivity but also allows pharmacies to meet the growing demands of personalized medication compounding:
- Enhance precision in ingredient measurement.
- Reduce the risk of human error in compounding processes.
- Facilitate quicker turnaround times for patient prescriptions.
- Improve workflow efficiency within pharmacy operations.
The right equipment makes compounding precise and efficient. Yet, the safety of the lab and compliance with regulations must not be overlooked—these tools keep both the pharmacist and the patient secure.
Safety Equipment and Compliance Tools in the Compounding Lab
In the compounding lab, safety equipment and compliance tools are essential for protecting pharmacy staff and ensuring quality in medication preparation. I will discuss the importance of personal protective equipment (PPE) for pharmacists, effective ventilation systems to maintain air quality, cleanroom supplies for contamination control, waste disposal units for hazardous materials, and compliance software for documentation and tracking. Each component plays a significant role in fostering a safe and efficient work environment.
Personal Protective Equipment for Pharmacists
In my role as a pharmacy consultant, I’ve seen firsthand how essential personal protective equipment (PPE) is for pharmacists working in compounding labs. Wearing appropriate PPE, such as gloves, masks, and goggles, protects pharmacy personnel from harmful chemicals and potential contaminants while they handle hazardous materials. Ensuring that all staff members are well-equipped with high-quality PPE not only fosters a safer working environment but also helps maintain compliance with safety regulations set forth by health authorities.
Moreover, I recommend regular training sessions on the proper use and importance of PPE in the compounding process. Many pharmacists may underestimate the risks associated with chemical exposure or contamination. By emphasizing the necessity of PPE and providing practical examples of safe practices, pharmacies can empower their teams to prioritize safety and adhere to industry standards effectively. This proactive approach significantly reduces the likelihood of accidents and enhances overall operational safety in compounding environments.
Ventilation Systems to Maintain Air Quality
In my experience as a pharmacy consultant, effective ventilation systems are essential for maintaining air quality in compounding labs. They help remove harmful vapors and airborne particles that can compromise both worker safety and the integrity of compounded medications. By implementing a well-designed ventilation system, pharmacies can provide a safer environment that enhances compliance with health regulations.
Regular maintenance and monitoring of ventilation systems are crucial to ensure their effectiveness. I recommend conducting routine checks to verify air flow rates and filter conditions, which supports optimal performance. Additionally, integrating alarms and sensors can help pharmacy staff be alerted to any changes in air quality, allowing for prompt corrective action:
- Remove harmful vapors effectively.
- Enhance safety for pharmacy staff.
- Monitor air flow rates consistently.
- Integrate alarms for immediate alerts.
Cleanroom Supplies for Contamination Control
In my consultations with pharmacies, I’ve seen the importance of having adequate cleanroom supplies for effective contamination control. Items such as sterile gloves, bouffant caps, and shoe covers are critical in maintaining a clean environment, preventing any external contaminants from entering the workspace. By ensuring that all personnel are equipped with these supplies, we can significantly reduce the risk of contamination during the compounding process.
Additionally, using sterile wipes and disinfectants regularly within the cleanroom enhances safety and helps meet compliance standards. I’ve found that establishing a routine cleaning protocol, which includes sanitizing surfaces and equipment, is essential for any compounding pharmacy. This proactive approach not only safeguards the quality of compounded medications but also reinforces a culture of safety and responsibility among staff members.
Waste Disposal Units for Hazardous Materials
In my experience, waste disposal units for hazardous materials are vital to maintaining a safe compounding environment. These units are designed specifically to handle pharmaceutical waste, ensuring that hazardous substances are disposed of in compliance with health regulations. By using these specialized containers, pharmacies can prevent contamination and exposure, reducing risks not only for staff but also for patients.
Implementing a systematic approach to hazardous waste disposal is crucial in any pharmacy. I recommend regular training for staff on how to segregate hazardous materials correctly and understand the usage of waste disposal units. This proactive measure enhances compliance with local and federal regulations while ensuring that pharmacy operations run smoothly and safely:
- Use specialized waste disposal units for pharmaceutical waste.
- Train staff on proper waste segregation and disposal protocols.
- Regularly monitor and maintain waste disposal systems.
Compliance Software for Documentation and Tracking
In my experience as a pharmacy consultant, compliance software serves as a critical asset in documenting and tracking pharmacy operations, especially in compounding environments. This software not only enhances oversight of medication preparation processes but also ensures adherence to regulatory standards, which is crucial for patient safety. By utilizing these tools, pharmacies can maintain accurate records of compounded medications, including ingredient sources and dosage forms, thereby minimizing the risk of errors and improving transparency in operations.
Moreover, compliance software streamlines the auditing process by consolidating documentation in a centralized system. I have seen firsthand how this facilitates easier access to information during inspections or audits, significantly reducing stress for pharmacy staff. By implementing a robust compliance software solution, pharmacies can enhance their operational efficiency, allowing team members to focus more on patient care rather than paperwork, which ultimately leads to improved service quality and adherence to both state and federal regulations.
The compounding lab thrives on safety and precision, but tools alone cannot do the work without proper care. Let’s now explore how to maintain and nurture this vital equipment to keep it ready for the task at hand.
Maintenance and Care of Compounding Tools and Equipment
Proper maintenance and care of compounding tools and equipment are essential for ensuring efficient pharmacy operations and safeguarding patient health. I’ll discuss cleaning protocols that preserve equipment integrity, calibration techniques that ensure consistent accuracy, and proper storage solutions for longevity. Additionally, regular equipment inspections and servicing, along with the benefits of vendor support and service agreements, will be highlighted to reinforce the importance of proactive maintenance in your compounding practices.
Cleaning Protocols to Preserve Equipment Integrity
In my role as a pharmacy consultant, I cannot stress enough the importance of establishing rigorous cleaning protocols for compounding tools and equipment. Regular cleaning not only minimizes contamination risks but also extends the lifespan of valuable assets like mortars, pestles, and precision balances. I’ve witnessed how implementing simple yet effective cleaning techniques, such as using sterile wipes and appropriate disinfectants, can significantly enhance the operational integrity of compounding environments.
To maintain equipment integrity, I recommend creating a comprehensive cleaning schedule that adheres to regulatory guidelines. Each piece of equipment should have specific cleaning instructions tailored to its material and use case. Incorporating best practices, like testing cleaning solutions for compatibility and ensuring thorough drying before storage, can help prevent degradation and ensure accuracy in future compounding tasks. A well-maintained workspace ultimately encourages adherence to safety standards and supports high-quality medication preparation:
- Establish rigorous cleaning protocols for all compounding tools.
- Utilize sterile wipes and compatible disinfectants for effective sanitation.
- Create and follow a comprehensive cleaning schedule for equipment.
- Ensure drying of equipment before storage to maintain integrity.
- Regular maintenance supports safety and quality in medication preparation.
Calibration Techniques for Consistent Accuracy
Calibration of compounding tools, particularly precision balances, is essential for maintaining accuracy in medication preparation. In my experience, I recommend conducting routine calibrations at specified intervals to ensure these tools consistently provide accurate measurements. This process not only minimizes errors during compounding but also complies with regulatory standards set by organizations such as the United States Pharmacopeia, thereby safeguarding patient health.
To effectively calibrate equipment, pharmacies should establish a clear protocol that involves using certified calibration weights to verify accuracy. Additionally, I suggest keeping a log of calibration dates and results to track performance over time. This methodology not only promotes accountability but also helps identify any trends that may indicate equipment wear or malfunction, further supporting precise compounding practices:
- Establish a calibration schedule for precision equipment.
- Use certified calibration weights for accurate measurements.
- Maintain a log of calibration dates and results.
- Monitor equipment performance to identify potential issues.
- Ensure compliance with industry standards for patient safety.
Proper Storage Solutions for Longevity
Proper storage solutions are essential for maintaining the longevity of pharmacy compounding tools and equipment. I recommend storing items in a clean, dry environment away from direct sunlight to prevent degradation. For delicate instruments like precision balances, consider using protective cases to shield them from dust and accidental damage, ensuring their accuracy remains uncompromised.
Organizing compounding tools in designated storage areas can greatly enhance efficiency and safety in the pharmacy. I found that implementing a labeling system for shelves and drawers not only keeps equipment readily accessible but also reduces the risk of cross-contamination. By following structured storage practices, pharmacies can preserve their equipment’s lifespan and ensure a safe compounding environment:
- Store tools in a clean, dry environment.
- Use protective cases for delicate instruments.
- Implement a labeling system for organized storage.
- Keep frequently used items easily accessible.
Regular Equipment Inspections and Servicing
In my experience as a pharmacy consultant, regular equipment inspections are essential for upholding the integrity of compounding tools and equipment. By systematically checking each piece for wear, damage, or functionality issues, pharmacies can ensure that they operate efficiently and safely. This proactive approach prevents equipment-related disruptions that could compromise patient safety and medication accuracy.
I also emphasize the importance of servicing compounding equipment at appropriate intervals. For instance, precision balances need routine professional calibration to maintain their accuracy, while high-speed homogenizers may require periodic maintenance to keep them functioning optimally. Implementing a regular inspection and servicing schedule not only extends the lifespan of your equipment but also reinforces compliance with regulatory standards, ultimately supporting high-quality pharmaceutical care.
Vendor Support and Service Agreements Benefits
In my experience as a pharmacy consultant, vendor support and service agreements are vital for maintaining the integrity and functionality of compounding tools and equipment. These agreements often include regular maintenance checks, which help to identify and rectify issues before they can disrupt pharmacy operations. By establishing a relationship with a reliable vendor, I have found that pharmacies can ensure their equipment is compliant with regulatory standards and remains in optimal working condition.
Furthermore, service agreements often provide training and support for pharmacy staff, helping them to understand the best practices for using and maintaining their equipment. This proactive approach not only enhances operational efficiency but also fosters a culture of safety and quality within the pharmacy. When pharmacies prioritize these vendor partnerships, they position themselves for success in delivering high-quality compounded medications to their patients:
- Regular maintenance checks to prevent equipment disruptions.
- Enhanced staff training for optimal equipment use.
- Compliance with regulatory standards through vendor support.
Caring for your compounding tools keeps them sharp and ready. But choosing the right suppliers for your compounding accessories can elevate your practice even further.
Selecting the Right Suppliers for Compounding Accessories
When selecting suppliers for compounding accessories, I focus on several key factors to ensure optimal performance and value. I assess equipment quality and durability to guarantee reliability, while also comparing costs without compromising on quality. Evaluating supplier customer support is crucial for ongoing assistance, and I find reading industry reviews and testimonials valuable for insights. Understanding warranty and return policies further safeguards investment and ensures peace of mind.
Assessing Equipment Quality and Durability
When I evaluate suppliers for compounding accessories, the quality and durability of their equipment are paramount. I focus on materials known for their robustness and resistance to wear, as this directly impacts the reliability of compounding processes. Choosing well-manufactured tools reduces the chances of equipment failure, ensuring consistency in medication preparation and adhering to safety standards.
Additionally, I recommend reviewing product specifications and warranty conditions to gauge both quality and durability thoroughly. Suppliers that offer extensive warranties demonstrate confidence in their products and support their commitment to quality. This assurance can protect your investment while enhancing operational efficiency in your pharmacy.
- Assess materials for robustness and wear resistance.
- Choose suppliers with comprehensive warranty options.
- Review product specifications for quality assurance.
Comparing Costs Without Compromising Quality
In my experience as a pharmacy consultant, effectively comparing costs while ensuring quality can significantly impact your operation’s efficiency. When selecting suppliers for compounding accessories, I focus on evaluating the long-term value of the equipment rather than just the initial purchase price. For instance, investing in high-quality precision balances might come with a higher upfront cost, but their accuracy and durability can reduce the frequency of replacements and related disruptions in your compounding processes.
Moreover, I find that seeking suppliers who offer warranty coverage and robust customer support can provide additional value. Reliable suppliers are not just selling products; they should also support your pharmacy’s needs through guidance and assistance. This way, while I’m keeping an eye on costs, I ensure that my pharmacy is aligned with suppliers who prioritize quality and ongoing support, ultimately enhancing our compounding capabilities and maintaining patient safety.
Evaluating Supplier Customer Support
When I evaluate suppliers for compounding accessories, I always prioritize their customer support quality. Strong customer support can significantly enhance the experience of using their products, especially if issues arise. For instance, reliable suppliers offer prompt responses to inquiries and provide thorough guidance on equipment usage and maintenance, which is crucial for ensuring compliance and operational efficiency.
Additionally, I believe it’s important to choose suppliers who offer extensive training resources and troubleshooting assistance. A robust support system ensures that my team can resolve any challenges without significant downtime, ultimately enhancing our compounding capabilities. By fostering a solid relationship with our suppliers, we can gain deeper insights and assistance that directly contribute to patient safety and quality in our pharmacy operations.
Reading Industry Reviews and Testimonials
When selecting suppliers for compounding accessories, I have found that reading industry reviews and testimonials is crucial for making informed decisions. These insights often highlight the experiences of other pharmacy professionals, providing valuable perspectives on equipment quality, reliability, and customer support. By focusing on genuine feedback, I can better assess which suppliers consistently meet the needs of pharmacies like mine, ensuring that we invest in tools that enhance our compounding operations.
Additionally, industry reviews can uncover potential issues that may not be immediately apparent during initial evaluations. For example, reviews may point out how effectively a supplier resolves problems or provides training resources, which is vital for maintaining compliance and operational efficiency. By incorporating these firsthand accounts, I can choose partners who not only offer high-quality products but also contribute to a safer and more productive compounding environment in my pharmacy.
Understanding Warranty and Return Policies
When choosing suppliers for compounding accessories, understanding warranty and return policies is vital. I often advise pharmacies to examine the terms of these policies carefully, as they can provide insight into the quality and reliability of the equipment. For instance, a supplier offering an extended warranty may indicate confidence in their products, suggesting that they are committed to ensuring your investment is protected against defects or malfunctions.
Additionally, a clear and fair return policy can significantly ease concerns over whether a supplier’s products will meet your specific needs in a compounding environment. I recommend looking for suppliers who allow returns within a reasonable timeframe and have a straightforward process for handling issues. This approach not only helps you manage risks associated with your purchases but also reinforces trust in your supplier’s commitment to customer satisfaction and operational efficiency.
Choosing reliable suppliers is just the beginning. In the ever-evolving world of pharmacy compounding, new tools and equipment beckon, promising to reshape how we work and improve patient care.
Future Trends in Pharmacy Compounding Tools and Equipment
In navigating the future of pharmacy compounding, I identify key trends shaping our profession. Embracing automation will streamline compounding processes, while the rise of 3D printing offers innovative methods for medication preparation. Integrating digital technologies with compounding equipment enhances precision, and eco-friendly solutions promote sustainability. Additionally, we must adapt to evolving regulatory changes impacting our tools and practices.
Embracing Automation in Compounding Processes
Embracing automation in pharmacy compounding processes is transforming how we prepare medications. By integrating automated compounding devices, pharmacies can streamline workflows, reduce preparation time, and enhance dosing accuracy. I’ve seen firsthand how these innovations not only minimize the risk of human error but also improve overall operational efficiency, allowing pharmacy staff to focus on patient care and other critical tasks.
In my experience, automation tools such as high-speed homogenizers and robotic filling systems can significantly increase output while maintaining the high quality expected in pharmaceutical compounding. As regulations continue to evolve, these automated solutions provide scalable options that adhere to safety standards, ensuring compliance without sacrificing productivity. With the right technology, pharmacies can meet growing patient demands while advancing their compounding capabilities effectively.
The Rise of 3D Printing in Medication Preparation
The rise of 3D printing in medication preparation represents a significant advancement in pharmacy compounding, enabling customized drug formulations tailored to individual patient needs. In my experience, this technology allows for the creation of complex dosage forms that may not be readily available on the market, addressing specific medical conditions or unique patient requirements. For instance, I have seen pharmacies successfully utilize 3D printing to produce personalized pediatric medications with accurate dosages and appealing flavors.
As I continue to explore the implications of 3D printing in pharmacy, I recognize its potential to enhance efficiency and reduce waste in medication preparation. This technology not only allows for on-demand production but also facilitates rapid prototyping of new formulations, ensuring that pharmacists can respond quickly to patient prescriptions. I believe that embracing 3D printing can streamline operations and significantly increase the capability of compounding pharmacies to meet patient needs effectively:
- Customized drug formulations tailored to individual needs.
- Rapid production and prototyping of new medications.
- Improved efficiency and reduced waste in medication preparation.
Integrating Digital Technologies With Equipment
Integrating digital technologies with compounding equipment represents a transformative shift in how pharmacies operate. With advancements such as software that tracks medication preparation and inventory management systems, I have observed a marked improvement in workflow efficiency and accuracy. Digital tools not only streamline the compounding process but also provide crucial data analytics that support better decision-making and allow for quick adjustments based on real-time information, ultimately enhancing patient safety and compliance with industry regulations.
Moreover, incorporating digital technologies can significantly reduce the potential for human error during the compounding process. For instance, I have seen firsthand how automated systems that interface with precision balances or capsule filling machines ensure accurate dosing and minimize the risks associated with manual handling. This integration enhances not only operational productivity but also fosters a more precise and reliable medication preparation environment, addressing the growing needs of pharmacies to deliver high-quality compounded medications efficiently.
Eco-Friendly Equipment and Sustainable Practices
As I observe the evolving landscape of pharmacy compounding, I see an increasing emphasis on eco-friendly equipment and sustainable practices. Pharmacies are beginning to adopt tools made from recyclable materials or designed to minimize waste, aligning their operations with environmental goals. This shift not only demonstrates a commitment to sustainability but also allows pharmacies to address the growing demand from patients who are increasingly conscientious about the planet’s health.
Moreover, implementing energy-efficient practices in compounding processes can directly contribute to reducing operational costs. For instance, I recommend that pharmacies explore the use of energy-saving devices and regular equipment maintenance, which can enhance performance while consuming less power. By integrating these eco-friendly solutions, pharmacies not only improve their bottom line but also position themselves as responsible stewards within their communities, further enhancing their reputation and trust among patients.
Adapting to Regulatory Changes Impacting Tools and Equipment
In my experience, adapting to regulatory changes in pharmacy compounding is crucial for maintaining compliance and ensuring patient safety. Regulations can change frequently, impacting everything from the types of compounds we can prepare to the equipment we use. Staying informed through continuous education and actively participating in relevant professional organizations helps me keep up with these changes, allowing my pharmacy to adjust practices and tools accordingly without compromising quality.
Moreover, I’ve found that regularly reviewing and updating our standard operating procedures (SOPs) is an effective way to align with new regulations. This practice ensures that our staff is well-versed in the latest compliance requirements and use of compounding equipment. By fostering a culture of compliance within the pharmacy, we not only enhance operational efficiency but also strengthen our commitment to providing safe and effective medications to our patients.
Conclusion
The comprehensive guide to pharmacy compounding tools and equipment highlights their essential role in ensuring safety, efficiency, and compliance in medication preparation. By investing in quality tools such as mortars, spatulas, precision balances, and automated devices, pharmacies can enhance operational workflows and minimize human error. Staying informed about advanced equipment and adhering to maintenance best practices not only supports regulatory compliance but also fosters a culture of safety and quality. Overall, prioritizing the right compounding tools empowers pharmacies to deliver accurate and effective medications tailored to patient needs, reinforcing their commitment to healthcare excellence.
Share This Story, Choose Your Platform!
Get In Touch
Phone: (847) 722-6942
Email: sales@end2endlogix.com
Web: end2endlogix.com